Rückblick auf die erste Förderperiode 2006 - 2010
|
Teilprojekt A2
Mikrostrukturierung und Integrationstechnologie für Piezofasern in metallische Trägerwerkstoffe (Blech)
Leiter:
Univ-Prof. Dr.-Ing. Andreas SchubertTechnische Universität Chemnitz
Institut für Werkzeugmaschinen und Produktionsprozesse
Professur Mikrofertigungstechnik
09107 Chemnitz
Telefon: 0371 / 531 34580
Telefax: 0371 / 531 34581
E-Mail: andreas.schubert@mb.tu-chemnitz.de
apl. Prof. Dr.-Ing. Dieter Weidlich
Technische Universität Chemnitz
Institut für Werkzeugmaschinen und Produktionsprozesse
Professur Werkzeugmaschinenkonstruktion und Umformtechnik
09107 Chemnitz
Telefon: 0371 / 531 23500
Telefax: 0371 / 531 23509
E-Mail: wzm@mb.tu-chemnitz.de
Forschungsgegenstand des Teilprojekts A2 ist das Auffinden und Erproben prototypenfähiger Mechanismen für die Erschließung einer Technologie zur großserienfähigen Fertigung von Piezo-Metall-Modulen durch direkte Integration und Ankopplung von Piezoelementen in mikrostrukturierte Aluminium-Bleche mit Verzicht auf elastische Zwischenschichten. Die Aktivitäten umfassen die Erforschung umformtechnischer Verfahren zur Mikrostrukturierung, serienfähiger Technologien zur Präzisionsmontage, Verfahren zum definierten Fügen und die Herstellung von Demonstratormodulen zur Entwicklung einer großserienfähigen Prozesskette in einem späteren Zeitraum.
Es wurde zunächst gemäß dem Anspruch einer direkten Integration von Piezoelementen in Aluminiumbleche ein Konzept für einen Technologie-Demonstrator mit Mikrokavitäten im Trägermaterial und stabförmigen Piezoelementen mit Rechteckquerschnitt erarbeitet. Der dargestellte Aufbau des Piezo-Metall-Modul nutzt den piezoelektrischen Longitudinaleffekt (d33-Effekt). Die Übertragung der mechanischen Kraft erfolgt daher parallel zum angelegten elektrischen Feld normal zu den Kontaktflächen.
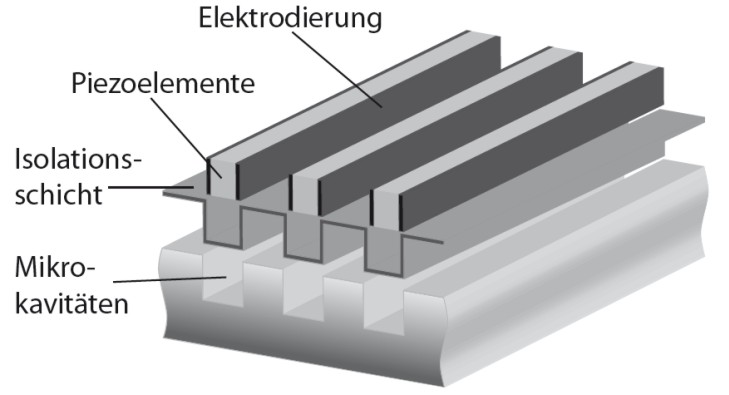
Bild: | Konzept für Piezo-Metall-Modul mit direkt integrierten Piezoelementen in mikrostrukturiertem Aluminium-Blech |
Im ersten Projektzeitraum stellt die Erforschung von Technologien zur Erzeugung präziser und anforderungsgerechter Mikrostrukturen auf der Oberfläche von Aluminium-Bauteilen eine große Herausforderung dar. Die zu erforschenden Mikrostrukturierungsverfahren müssen hierbei bereits das Potential für eine Serientauglichkeit besitzen. Zum Einsatz kommende Mikroumformtechniken sollen eine großflächige Abformung gewährleisten und dabei die mechanischen Kenngrößen des Trägerwerkstoffes Aluminium möglichst gleichmäßig beeinflussen. Vorzugsweise sind prozesssichere Durchsetz- und Prägeverfahren mit hoher Ortsauflösung zu untersuchen.
Die Grundlage zur Auslegung der Strukturierungsprozesse sowie die Entwicklung entsprechender Werkzeugsysteme zur Mikrostrukturierung bildet die Definition des Modul-Designs. In Kooperation der an der Prozesskette Blechumformung beteiligten Teilprojekte wurden die Abmaße der Piezoelemente (b=h=0,25 mm) sowie angestrebten Schichtdicken der Elektrodierung (1 µm) und Isolationsschicht (5 µm) festgelegt. Darauf Aufbauend wurden die geometrischen Abmaße des metallischen Trägers, unter Berücksichtigung von prozessbedingten Aufmaßen für die Erzeugung der Fügeverbindung, abgeleitet und festgelegt. Die Breite und Tiefe der Kavität beträgt 0,3 mm bei einer Länge von 10 mm. Der Abstand zwischen zwei Kavitäten beträgt 0,5 mm, woraus eine Stegbreite von 0,2 mm resultiert. Es soll eine Fläche von 10 x 20 mm² strukturiert werden. Als Versuchswerkstoffe wurden zwei für die Automobilindustrie relevante Aluminiumlegierungen (AlMg4,5Mn0,4 und AlSi1,2Mg0,4). Die Blechstärke variiert in einem Bereich von 0,8 mm bis 1,5 mm.
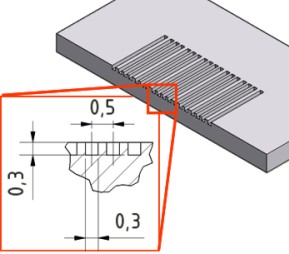
Bild: Schemadarstellung des mikrostrukturierten Bleches zur Herstellung des Piezo-Metall-Moduls
Auf Basis dieser Festlegungen wurden für die beiden zu untersuchenden Mikrostrukturierungsverfahren Durchsetzen und Fließpressen bzw. Prägen die Technologie erarbeitet und die Werkzeugsysteme konzipiert, konstruiert sowie realisiert. Beide Werkzeugsysteme besitzen einen modularen Aufbau. Daraus ergeben sich gerade im Bereich der Grundlagenforschung Vorteile, da die Werkzeugeigenschaften durch einfaches Austauschen der Aktivteile gezielt beeinflusst werden können. So kann zum Beispiel die Stempelstruktur an die jeweiligen Versuche durch einfaches Austauschen der Formsegmente angepasst werden. Ferner kann das Werkzeug nach den Umformversuchen beispielsweise zur Charakterisierung des Werkzeugverschleißes demontiert und anhand der einzelnen Segmente analysiert werden.
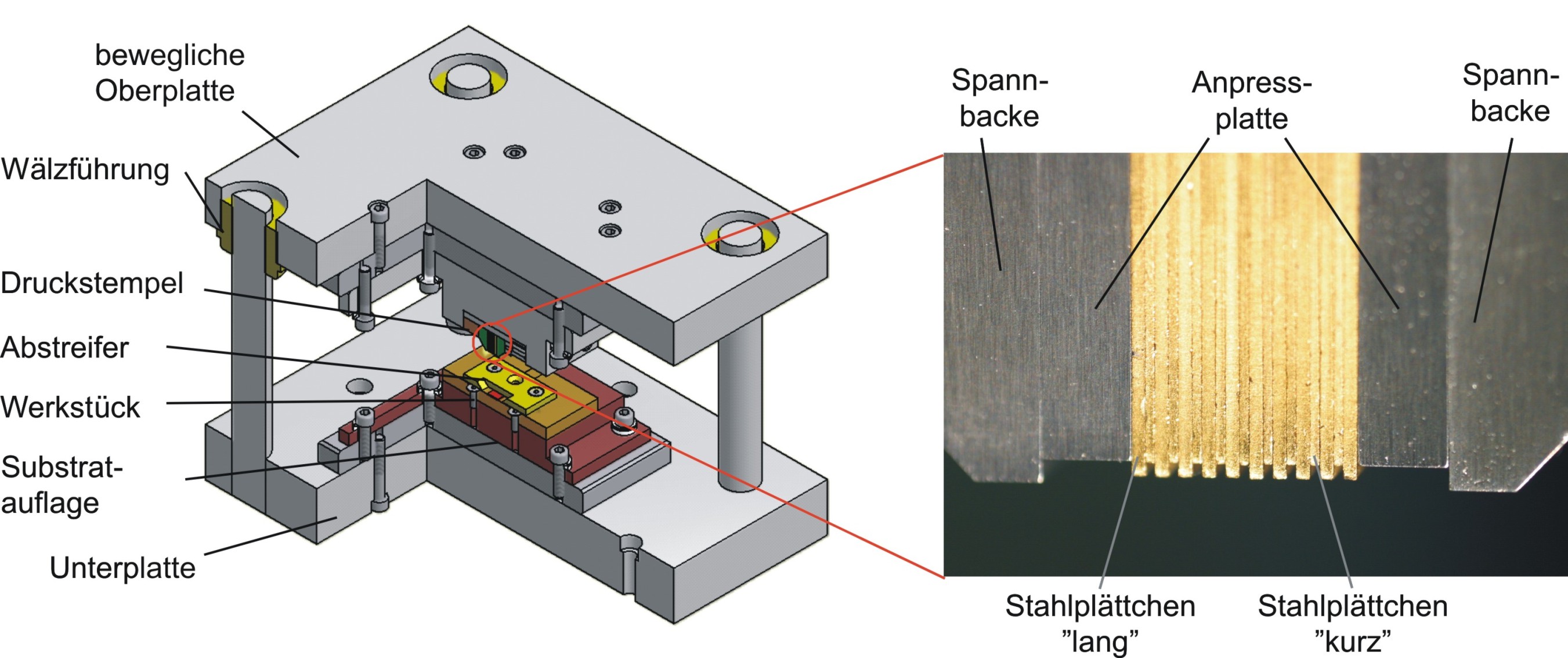
Bild: | Schematische Darstellung des Fließpresswerkzeuges (links); Detailfoto des modularen Werkzeugstempels (rechts) |
Die Ergebnisse der im ersten Antragszeitraum durchgeführten Grundlagenuntersuchungen zeigen bei beiden Verfahren ein hohes technisches Potential zur Herstellung von Mikrokavitäten-Arrays. Es kann mit beiden Fertigungstechnologien eine über den gesamten Bearbeitungsbereich gleichmäßige Strukturausbildung erreicht werden. Unabhängig von der Materialstärke können Kavitäten mit planer Grundfläche und nahezu senkrechten Seitenwänden erzeugt werden. Die Flanken der hergestellten Kavität zeichnen sich durch ein hohes Maß an Geradheit und Steilheit aus. Die quantitative Bewertung der erzeugten Strukturen zeigt, dass die Struktur des Stempels mit einer hohen Abbildegenauigkeit abgeformt werden kann.
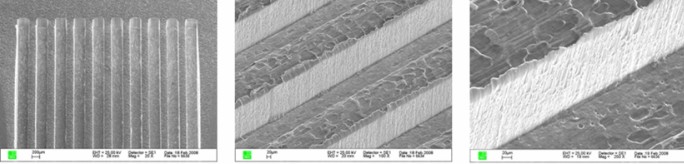
Bild: | Beispielhafte Umformergebnisse zum Fließpressen von Mikrokavitäten in AlMg4,5Mn0,4 bei einer Maximalkraft von 90 kN und einer Ausgangsblechdicke von 0,8 mm |
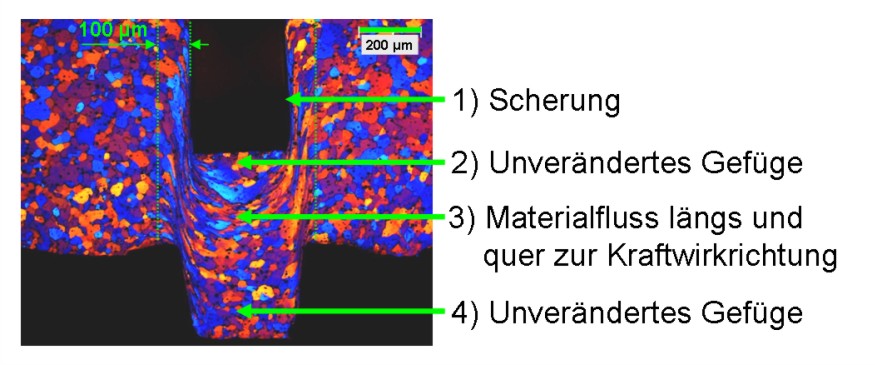
Bild: | Lichtmikroskopische Aufnahme des umgeformten Werkstoffgefüges am Beispiel einer mittels Durchsetzen erzeugten Kavität in AlSi1,2Mn0,4 (d0 = 1 mm) |
Ausgangsmaterial für die Integration der Piezoelemente bilden gesägte Platten aus Piezomaterial, welche auf einer Klebefolie vorliegen. Die Montageaufgabe besteht nun im Ablösen der bruchempfindlichen Piezoelemente von der Klebefolie sowie im Handhaben und Einlegen in die Mikrokavitäten.
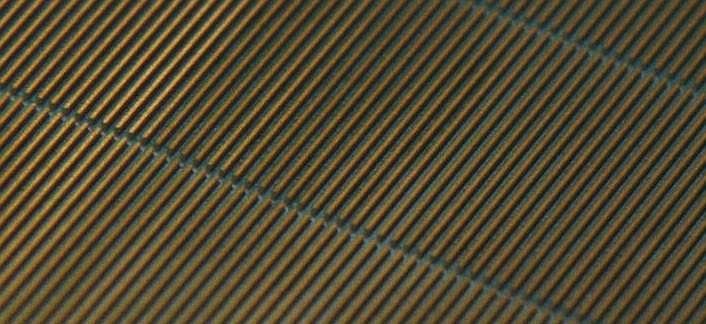
Bild: Piezostäbchen (Abmaße ca. 0,25 mm x 0,25 mm x 10 mm) auf Klebefolie
Auf Grundlage eines Vergleichs unterschiedlicher Montagekonzepte wurde eine miniaturisierte Versuchseinrichtung mit Präzisionslinear- und Rotationseinheiten und einer in die Greifereinheit integrierten Tripod-Parallelkinematik entwickelt. Darin werden unterschiedliche Greifprinzipien für die Handhabung von piezokeramischen Mikrobauteilen untersucht. Der modulare Aufbau ermöglicht ein schnelles Wechseln zwischen den verschiedenen Mikrogreifern.
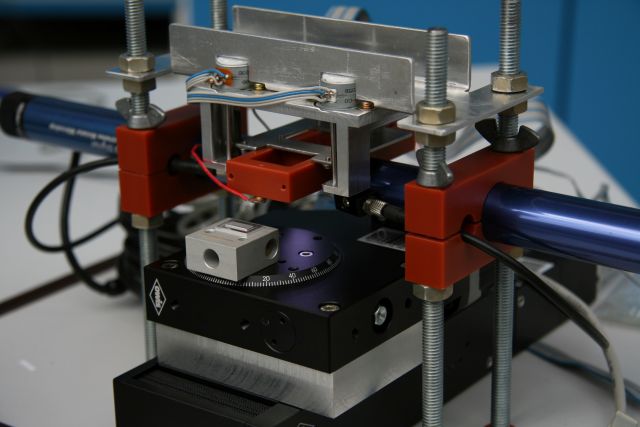
Bild: | Versuchsaufbau für die Präzisionsmontage von Piezoelementen in mikrostrukturierte Träger |
Der Montageprozess erfordert das Greifen der Piezostäbe nur an der Oberseite. Bisher haben sich dazu elektrostatische und Vakuum-Mikrogreifer in unterschiedlichen Ausführungsformen als geeignet erwiesen. Numerische Simulationen der auftretenden Greifkräfte bei der Handhabung mit elektrostatischen Greifern sind Grundlage für deren Dimensionierung. Beide Greifertypen wurden experimentell bezüglich ihrer Eignung für die Montageaufgabe untersucht. Eine mögliche Ausführung eines Vakuumgreifers besteht in dem abgebildeten Saugnadel-Greifer. Der Montageprozess kann durch hochauflösende Kamerasysteme beobachtet werden.br>
Bild: Saugnadelgreifer mit Piezoelement
Neben den Technologien zum Greifen wurde ein Automatisierungs- und Materialflusskonzept für das sequentielle Drehen und Einlegen von Piezoelementen entwickelt und ein Modell eines solchen miniaturisierten Produktionssystems liegt modellhaft in 3D-CAD vor. In Montageversuchen werden mithilfe der Versuchseinrichtung einzelne Piezoelemente in Mikrokavitäten eingelegt, sodass diese nachfolgend gefügt werden können.
Serientaugliche Fügeverfahren für ein sicheres Verankern der Piezoelemente im strukturierten Trägerwerkstoff sind ein weiteres Forschungsfeld im ersten Antragszeitraum. Vorzugsweise sind hierbei mechanische Fügeverbindungen mit Verzicht auf elastische Zwischenschichten zu erforschen.
Durch experimentelle Untersuchungen konnte nachgewiesen werden, dass eine kraftschlüssige Verbindung zwischen Piezoelement und Trägerwerkstoff durch umformtechnisches Verpressen erzeugt werden kann. Die Analyse der Fügeverbindung zeigt, dass sich das Material über die gesamte Länge der Kavität homogene an das Faserprofil anschmiegt. Bei Betrachtung der Oberfläche der verpressten Fasern sind keine Risse bzw. Ausbrüche im Piezomaterial erkennbar. Zur Begutachtung des Querschnittes wurden Schliffbilder entlang der verpressten Fasern angefertigt. Die Betrachtung der Profile zeigt, dass unabhängig von der Position ein zerstörungsfreies Fügen der Piezoelemente im metallischen Trägerwerkstoff möglich ist. Bei der optischen als auch rasterelektronenmikroskopischen Betrachtung konnten keine Bruchstellen bzw. keine Risse im Piezoelement festgestellt werden.
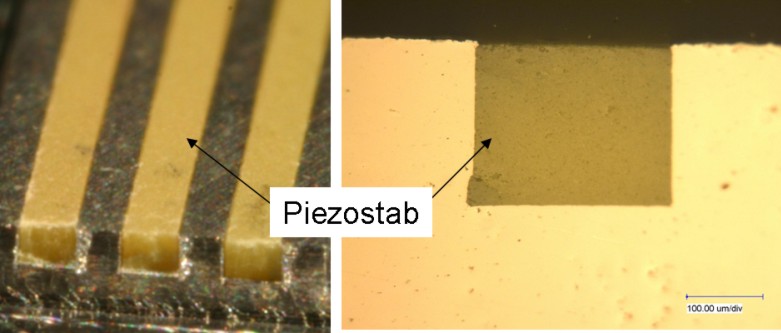
Bild: | Beispielhafte Ergebnisse zum Fügen von Piezoelementen in metallische Trägerkavitäten (ALMg4,5Mn0,4 d=1,5 mm) |