Work Groups
Head of Work Groups Work:
PD Dr.-Ing. Welf-Guntram DrosselFraunhofer-Institute for Machine Tools and Forming Technology IWU
Reichenhainer Str. 88
D-09126 Chemnitz
Telephone: +49-(0)371 / 5397-1304
Telefax: +49-(0)371 / 5397-1447
E-Mail: drossel@iwu.fraunhofer.de
In addition to commercially available piezoelectric modules, several internally developed modules will be integrated into the smart part and undergo testing. Such modules are the microstructured piezoelectric modules developed in subproject A2, the thermoplastic-compatible piezoceramic modules (TPM) from subproject A5 and the micro injection moulding piezoelectric modules (µIM) from subproject A6.
The polarisation and the contacting technologies of the modules are developed by the teams of subprojects C3 and A4, respectively. Subproject B2 deals with the numerical investigation of the forming operation including the modelling of the orthotropic structured piezoceramic modules, the floating support effect and the loading of the piezoelectric module.
Modelling of the curing process using an internally developed material model is the focus of subproject C7. Future work includes the integration of this model into the global forming simulation conducted by the team of subproject B2. Studies on the functionality and reliability of the piezo-metal-compounds are performed in the subprojects B1, B2 and C8.
The effects of forming on the polarisation of the integrated piezoelectric modules are investigated in subprojects C3 and C8. Further development of the modules will continue by conducting experiments and numerical simulations. The forming limits under a series of forming conditions and with different types of piezoelectric modules will be determined.
The main research focus of the process chain „fibre-reinforced polymers“ is on the design of active composite structures ready for series production by utilization of thermoplastic-compatible piezoceramic modules (A5, B4) as well as by the direct ma-terial integration of piezoceramic components into polyurethane composites by the novel multi-fibre-injection-technology (B6). Therefore, both current commercially available module designs are material adapted to thermoplastic matrix systems and novel piezoceramic fibre based modules are developed (A5, A1). Beside the question of material compatibility, mainly problems with regard to an integral design of the process chain are investigated. This includes for instance problems concerning the part inherent design of conductors and contacts for the transmission of energy and information (A4, A5, B4).
The verification of the part functionality and the continuous material homogeneous connection of the module components to the composites structure are done by the example of a PT-PIESA uniform plate (C6). By means of the acquired models with respect to the polarization behaviour of piezoceramic materials under temperature and pressure influences, the respectiveness of a thermo-mechanical load on the polarization process can be described and an efficient shifting of the polarization into the part production process (forming and consolidation) can be conducted (C3, B4). In order to proof the integrity and to analyze the state of deterioration of active composite structures, respectively, a non-destructive testing method based on the pyroelectric effect is developed (C8).
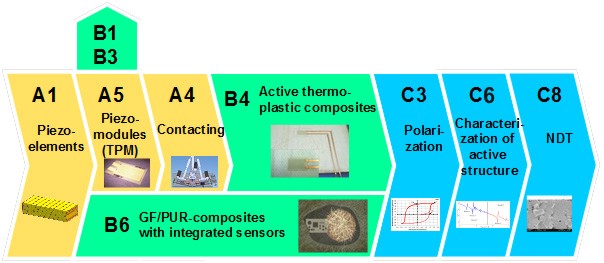
Fig. 1: Process chain “fibre-reinforced polymers”
The working group “Piezoceramic and Characterization” focuses on design, fabrication and characterization of piezoceramic components to be integrated into lightweight structures. Based on process chain demands topics on material aspects, design guidelines and investigation on effective material parameters are intensively discussed and transferred into technological processes. Piezoceramic modules based on piezoceramic fibers and plates are in the center of investigation.
Piezofiber composites based on piezoceramic fibers embedded in a polymer matrix will be integrated into the process chains “Forming” and “Fiber Composites”. Therefore, issues on geometrical size and arrangement of piezoceramic fibers within the polymer matrix, fiber-matrix-adhesion and electrical driving of the piezofiber composites are of great interest.
Piezoceramic laminates based on PZT plates integrated into low temperature cofired ceramic (LTCC) multilayers are developed to be embedded into metal matrices within the process chain “Casting”. Questions concerning form- and friction-locked integration, mechanical clamping by the surrounding metal matrix as well as termination of the LTCC/PZT modules are discussed.
One key aspect of the working group is the determination and interpretation of effective material data. Experimental and theoretical methods to measure the polarization state, mechanical strain and stress fields, the electrical impedance and the pyroelectric current under complex load conditions are developed. Generalized material laws are derived from experimental data in addition with FEM.
The working group consists of members of all process chains and meets one to two times a year.
![]() |
![]() |
|
Fig. 1: SEM cross section image of piezoceramic fibers in polymer matrix |
Fig. 2: X-ray image of LTCC/PZT module with electrical termination |
|
![]() |
![]() |
|
Fig. 3: Measurement setup utilized for the characterization of piezoceramic materials |
Fig. 4: Measurement setup for the characterization of pyroelectric response by means of thermal waves |