Subproject B2
Numerical study of the influence of forming operation on function of piezo-metal-compounds
Project Managers:
Prof. Dr.-Ing. habil. Prof. E. h. Dr.-Ing. E. h. Dr. h.c Reimund NeugebauerFraunhofer Institut for Machine Tools and Forming Technology
Reichenhainer Straße 88
09126 Chemnitz
telefone: +49-(0)371 / 5391-1401
telefax: +49-(0)371 / 5391-1404
E-Mail: reimund.neugebauer@iwu.fraunhofer.de
PD Dr.-Ing. Welf-Guntram DrosselI
Fraunhofer Institut for Machine Tools and Forming Technology
Reichenhainer Straße 88
09126 Chemnitz
telefone: +49-(0)371 / 5391-1304
telefax: +49-(0)371 / 5391-1447
E-Mail: welf-guntram.drossel@iwu.fraunhofer.de
Contact person
Dipl.-Ing. Sebastian HenselFraunhofer Institut for Machine Tools and Forming Technology IWU
Nöthnitzer Strasse 44
01187 Dresden
telefone: +49-(0)351 4772-2421
telefax: +49-(0)351 4772-2403
e-mail: sebastian.hensel@iwu.fraunhofer.de
Project overview
The microstructures of the piezo-patches cannot be taken into account in the global forming models, because an exact recreation of the ceramicfiber geometry and additional plastics components would lead to an expansive body discretization of the problem with impractical computation times. Hence for the piezo-patch a simplified homogenized orthotropic material model was applied. Basis for the homogenization is the investigation of the smallest cyclical repeated structural unit – the unit cell. The geometry for the submodel was determined from micrographs (Fig. 1). With the method of equivalence of elastic work [1, 2] the known material properties of the single components, e.g. fiber and plastics, are smeared with proper choice of unit load cases [3].
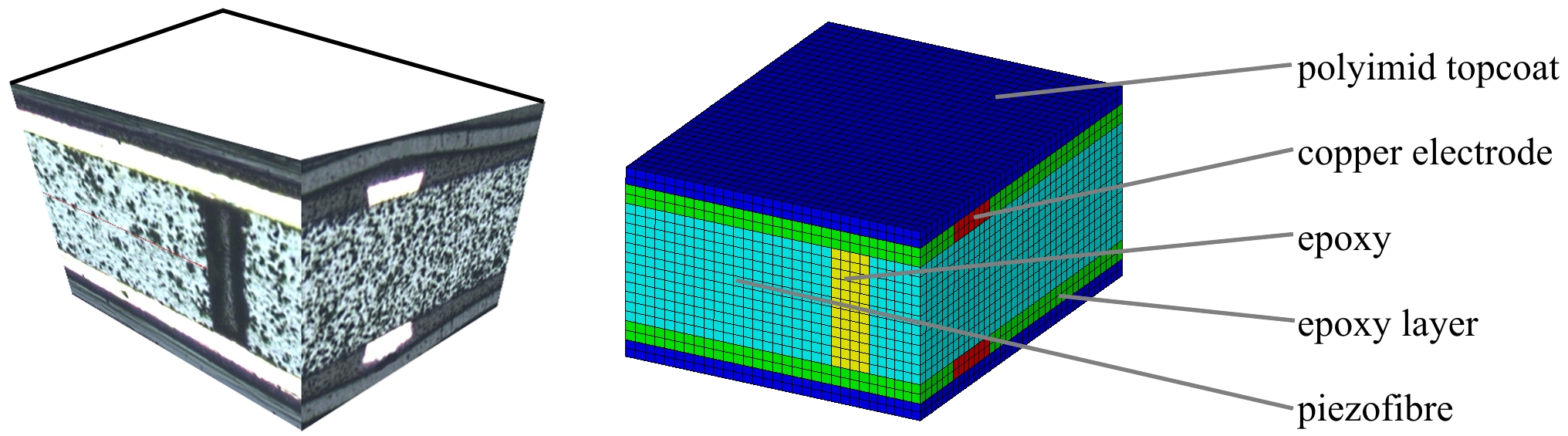
Fig. 1: Right: geometry model unit cell determined from micrographs of fiber structure (left)
After application (Fig. 2) and evaluation of the unit load case combinations, homogenized stiffness coefficients are provided and hence the engineering orthotropic linear-elastic material constants can be extracted.
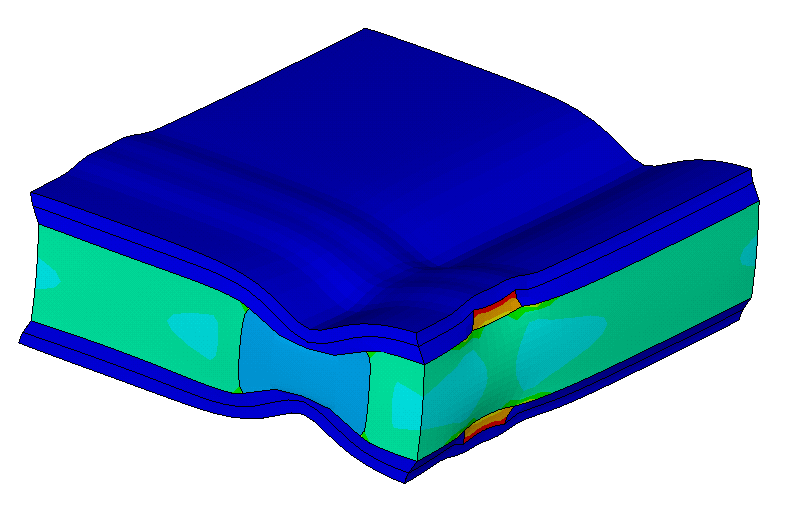
Fig. 2: Load case biaxial tension, deformations are plotted elevated
Based on the load cases of the homogenization, global stresses and strains of the homogenized material model in the forming simulation are transferred to the unit cell submodel to obtain and evaluate local loads, which act for instance on the piezo-fiber. With the computation of the fiber load level at each discretization point in the global model, a visualization of location-resoluted piezo-patch-loading is available [4].
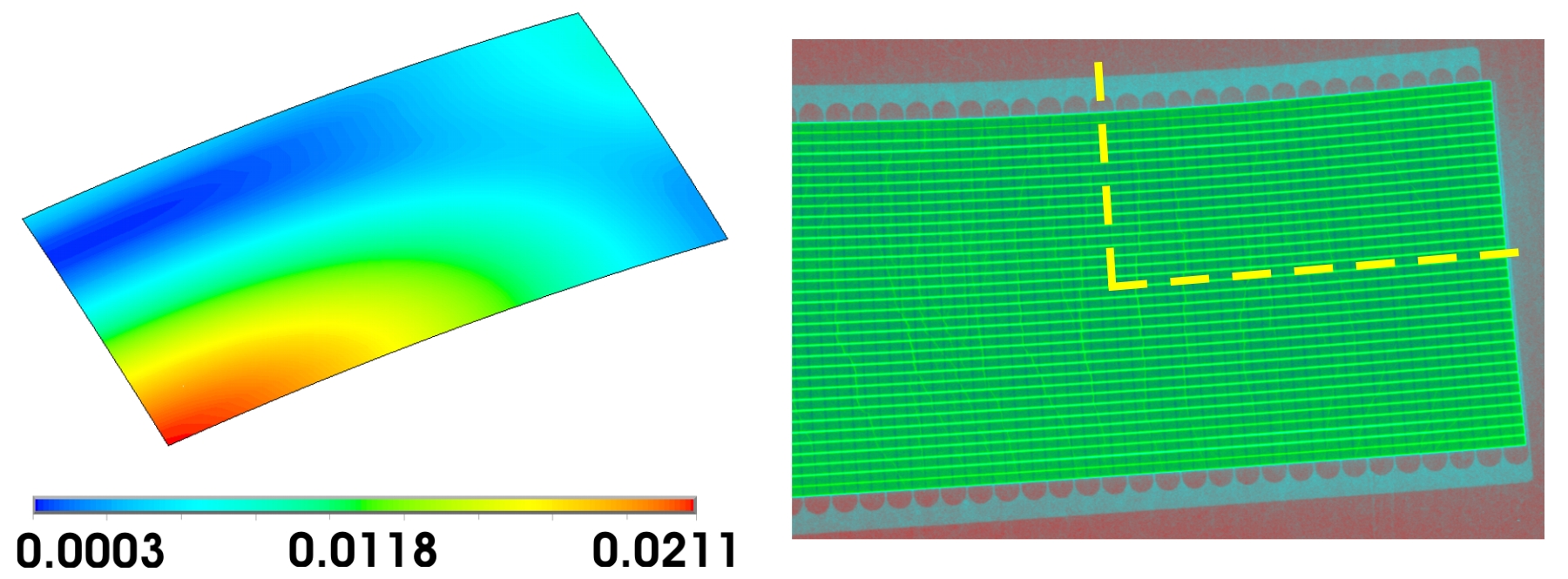
Fig. 3: Stretch drawing with punchradius of 50 mm, left: computed distribution of elastic work of the piezofibers
(1/4-model, corresponds to the area in the right picture defined by yellow lines),
right: X-ray-picture of formed piezo-patch located in the screened metal sheet part
If higher loadings of the piezo-patch with massive fiber-crack developments are reached, then the linear-elastic theory is not valid anymore. A prediction of probability of failure by means of numerical simulation is only possible with additional validated computations with similar load levels. Crack densities according to Fig. 4 cause a significant breakdown of patch functionality in the part. Minor fiber damage as shown in Fig. 3 affects the patch performance only less, because with the cyclic contacting electrodes sufficient fiber-volume can be addressed in spite of cracks.
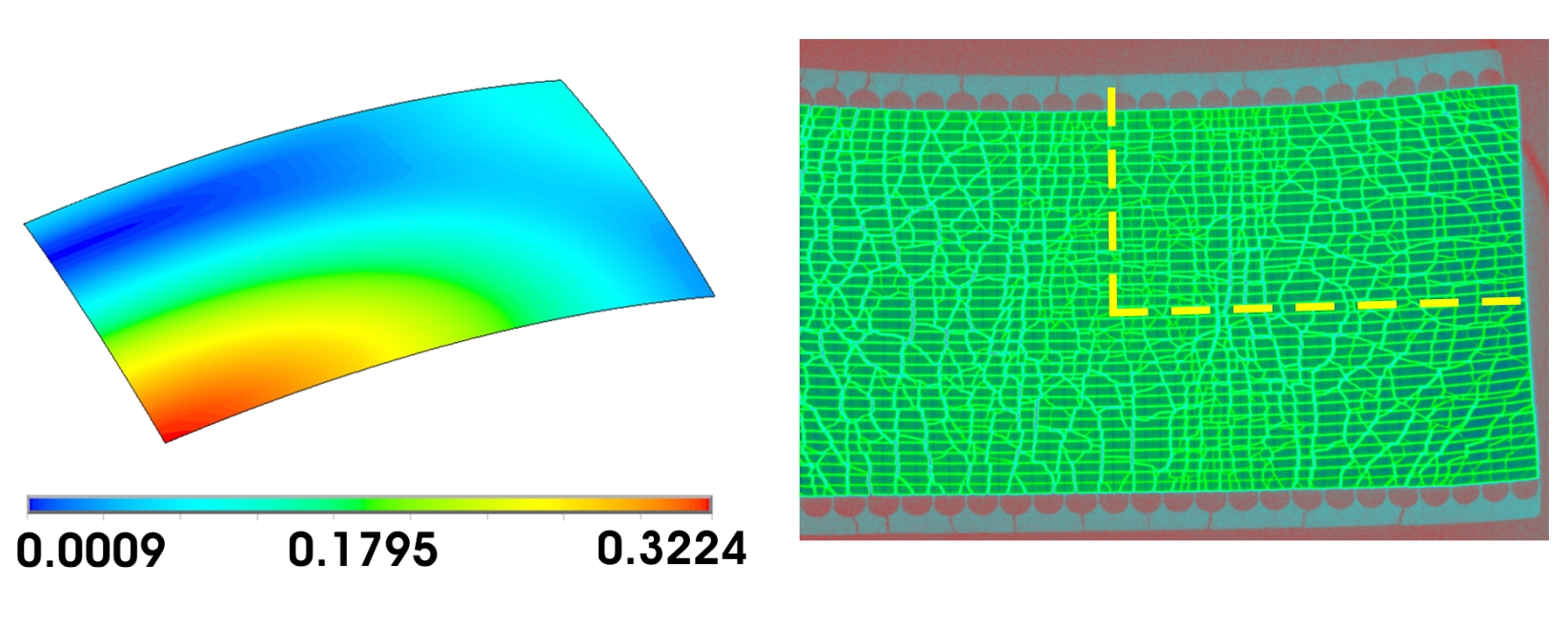
Fig. 4: Deep drawing with punchradius of 25 mm, left: computed distribution of elastic work of the piezofibers
(1/4-model, corresponds to the area in the right picture defined by yellow lines),
right: X-ray-picture of formed piezo-patch located in the screened metal sheet part
To describe the degradation and loss of performance of piezo-fiber-parts, in the second foundation period extensive experimental and numerical investigations are planned in the subproject B2. A decrease of performance, with respect to the arising load-combinations is continuously predictable by numerical simulation. For parts with a tolerable loss of functionality, higher degrees of deformation for the encapsulating metal sheets are achievable, which increases the variety of products. Moreover statements can be made with reference to sensitivity of the tolerance of patch position during forming.
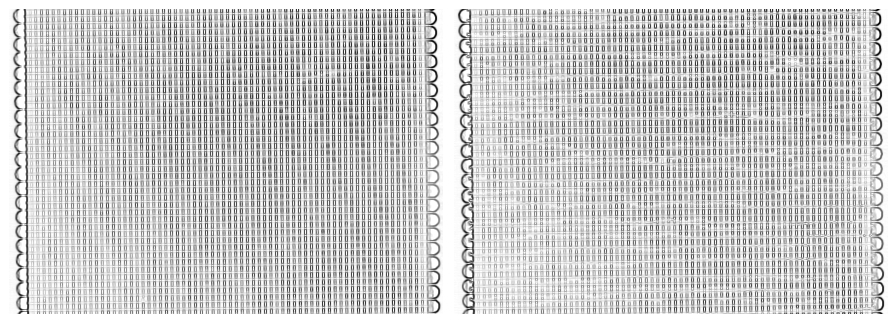
Fig. 5: Tension test piezo-patch with extensive crack development (left picture: before test, right picture: after test)
References of the project overview
[2] Kranz, B., Drossel, W.-G.: Rechnerische Beanspruchungsermittlung bei adaptiven Kompositen mit Piezokeramischen Fasern, Darmstadt 15./16.03.2006, DVM-Bericht 901, pp. 43-52
[3] R. Neugebauer, R. Kreißig, L. Lachmann, M. Nestler, S. Hensel, M. Flössel: Piezo-Module-Compounds in Metal Forming - Experimental and Numerical Studies; 8th International Conference in Mechatronics
2009, 18.11.2009 - 20.11.2009, Luhacovice, Czech Republic, August 2009
[4] Reimund Neugebauer, Lutz Lachmann, Welf-G. Drossel, Matthias Nestler, Sebastian Hensel: Multi-layer compounds with integrated actor-sensor-functionality, Production Engineering Research Development,
Production Engineering, Volume 4, Number 4 (2010), 379-384, DOI: 10.1007/s11740-010-0255-0