Subproject B3
Integration of piezoceramic modules into mertallic components by casting-technology and numerical simulation
Project Managers:
Prof. Dr.-Ing. Robert F. SingerUniversity of Erlangen-Nuremberg
Institute of Science and Technology of Metals
Martensstraße 5
91058 Erlangen
Telephon: +49-(0)9131 / 85 27530
Telefax: +49-(0)9131 / 85 27515
E-Mail: robert.singer@ww.uni-erlangen.de
Prof. Dr.-Ing. habil. Carolin Körner
University of Erlangen-Nuremberg
Institute of Science and Technology of Metals
Martensstraße 5
91058 Erlangen
Telephon: +49-(0)9131 / 82 27528
Telefax: +49-(0)9131 / 85 27515
E-Mail: carolin.koerner@ww.uni-erlangen.de
Contact:
Dipl.-Ing. Matthias SchwanklUniversity of Erlangen-Nuremberg
Institute of Science and Technology of Metals
Martensstr. 5
91058 Erlangen
Telephon.: +49-(0)9131 / 8527768
Telefax: +49-(0)9131 / 8527515
E-Mail: Matthias.Schwankl@ww.uni-erlangen.de
Dipl.-Ing. Alexander Klassen
University of Erlangen-Nuremberg
Institute of Science and Technology of Metals
Martensstr. 5
91058 Erlangen
Telephon.: +49-(0)9131 / 8528748
Telefax: +49-(0)9131 / 8527515
E-Mail: alexander.klassen@ww.uni-erlangen.de
Presenting the research program
In the first project stage, a novel supporting concept has been developed. The modules are surrounded by expanded metal consisting of Al99.5 (figure 1). This enables a complete integration and an eccentric module placement.
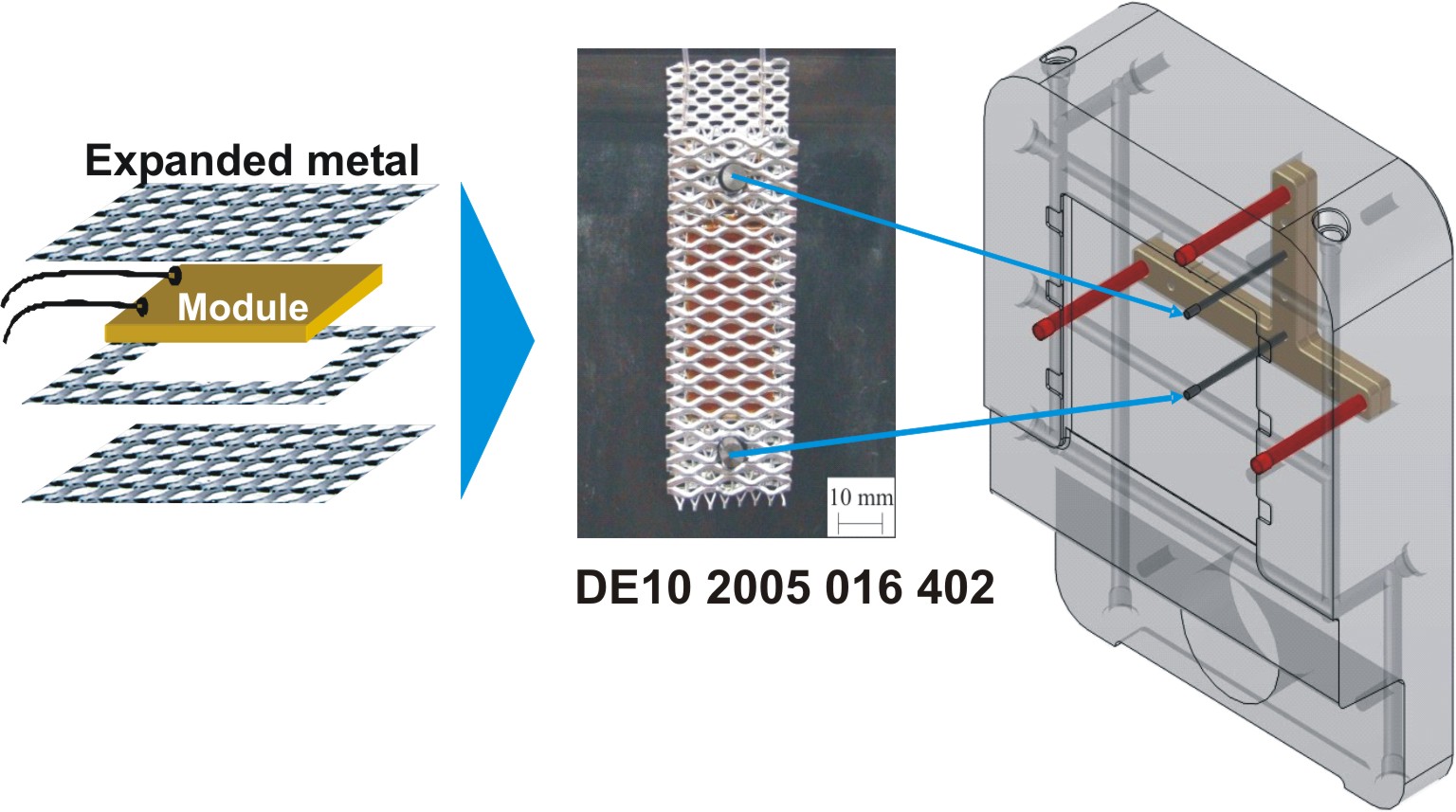
Fig. 1: The module is surrounded with expanded metal for positioning
and supporting. This package is placed onto ejector pins inside
the cavity of the mould.
Both structure and functionality of the module is retained in spite of the high loads (figure 2). Unfortunately, the interface strength between supporting structure and cast matrix is weak and the eccentric module placement is limited.
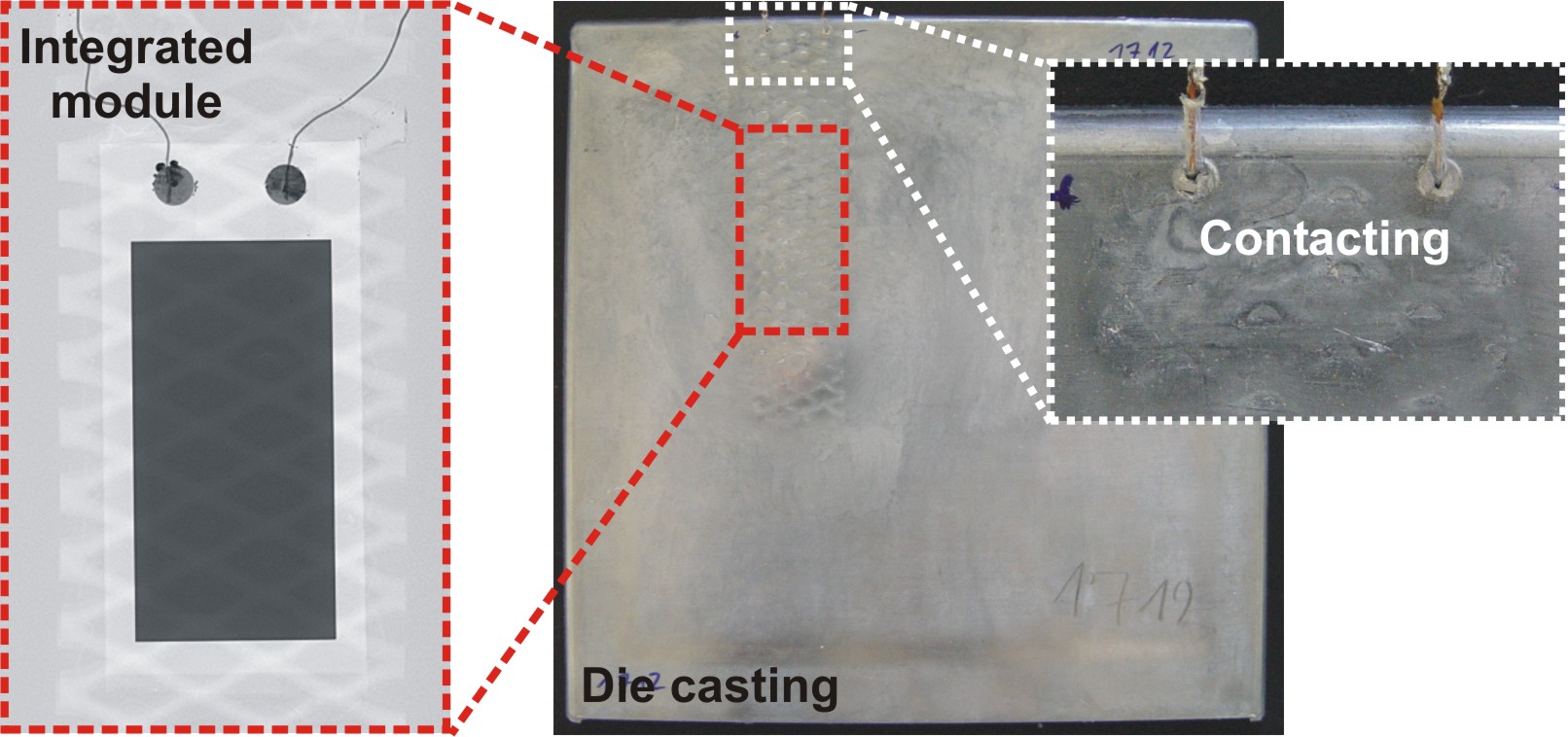
Fig. 2: Die casting with integrated PZT-module (red marked).
Contacting of the module is possible.
The aim of further research is the enhancement of the technology for a robust integration process suitable for mass production.
On the one hand, the interface strength between structure and cast matrix shall be improved. Therefore, a surface activation of the expanded metal is required to achieve a metallic continuity. On the other hand, the eccentric placement of the modules has to be modified to the end that the distance between module and neutral axis of the component is increased. This is essential for adaptronic applications.
The experimental studies are complemented by numerical simulations of the die filling and the infiltration of the expanded metal on the one hand and the thermo-mechanical response of the embedded PZT-module and the casting on the other hand. Melt flow simulations are carried out using the commercial VOF code Flow-3D. The numerical model (Fig. 3 and 4) enables the prediction of thermal and mechanical loads acting upon the module during the cavity fill and shall help to develop new module supporting strategies.
![]() |
![]() |
|
Fig. 3: Sensor-actuator-module and supporting structure (top). Schematic illustration of the numerical model (bottom). |
Fig. 4: Illustration of the die filling simulation and the infiltration process. |
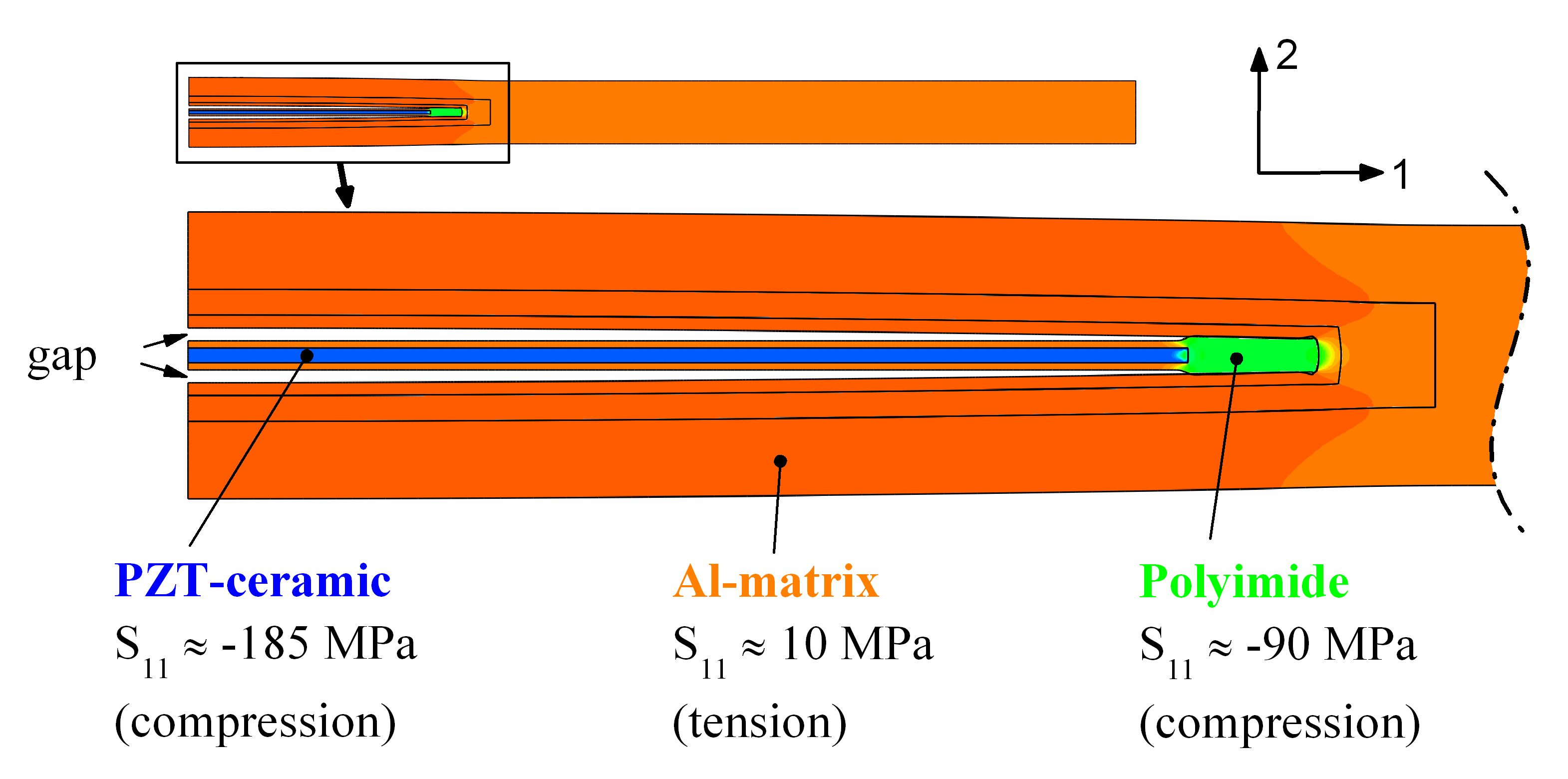
Fig. 5: Simulation of the thermo-mechanical behaviour of the aluminium matrix (orange)
and the module (blue) during the cooling process.