Subproject C6
Material Characterization and Numerical Simulation of Adaptiver Composites
Project Managers:
Prof. Dr.-Ing. Reinhard Lerch
Friedrich-Alexander-Universität Erlangen-Nürnberg
Lehrstuhl für Sensorik
Paul-Gordan-Str. 3/5
91052 Erlangen
Telephon: +49-(0)9131 / 85 23131
Telefax: +49-(0)9131 / 85 23133
E-Mail: reinhard.lerch@lse.eei.uni-erlangen.de
Dr. techn. Stefan Johann Rupitsch
Friedrich-Alexander-Universität Erlangen-Nürnberg
Lehrstuhl für Sensorik
Paul-Gordan-Str. 3/5
91052 Erlangen
Telephon: +49-(0)9131 / 85 23141
Telefax: +49-(0)9131 / 85 23133
E-Mail: stefan.rupitsch@lse.eei.uni-erlangen.de
Contact:
Dipl.-Ing. Jürgen Ilg
Friedrich-Alexander-Universität Erlangen-Nürnberg
Lehrstuhl für Sensorik
Paul-Gordan-Str. 3/5
91052 Erlangen
Telephon: +49-(0)9131 / 85 23143
Telefax: +49-(0)9131 / 85 23133
E-Mail: juergen.ilg@lse.eei.uni-erlangen.de
Presenting the Research Program
Motivation
The emphasis of the Collaborative Research Center/Transregio is on high-volume production-compatible production technologies for components with integrated piezo sensors and actuators. The development of manufacturing processes suitable for serial production demands a detailed characterization of the composites with regard to the electrical and mechanical properties. The standard procedure to determine material data of piezoceramics requires accurately manufactured test specimens with defined geometries. Since it is not possible to fabricate composites with the defined geometries, this standard procedure is not applicable in this case. In addition, this method allows no characterization of the passive (non piezoelectric) components of the composites. Therefore, the aim of this sub-project is to develop adequate methods to characterize the complete composite material.
Scientific objective
The characterization of the material properties (small signal parameters to describe the linear behaviour) is given by the piezoelectric basic equations, which describe the relations between the mechanical and electrical quantities. It is defined by the elasticity tensor, the dielectrical tensor and the piezoelectrical coupling tensor. The objective of this sub-project is to determine the non-vanishing entries of these tensors. In combination with the material density the tensor elements yield a complete characterization of the piezoceramic and consequently the composite. Hence, one can deduce important parameters like the mechanical and electrical impedance or the electromechanical coupling factor.
In addition, for a high-volume serial production, it is essential to determine the tolerance range of the material parameters and to investigate their temperature dependencies.
Concerning the actuatory application of the composites, one has to consider the nonlinear characteristics (large signal performance, hysteresis) when performing numerical simulations of the mechanical and electrical behavior. Therefore, another aim of this sub-project is to investigate different methods for macroscopic hysteresis modeling.
Methods
According to the state of knowledge at this time, a method to characterize all involved composite materials does not exist. Therefore, a novel method to determine all tensor elements will be developed based on the systematic approximation of simulation to measurement results. This so-called Inverse Method is a multi parameter optimization problem which minimizes the mean square deviation between measured and calculated data. The metrologically determinable quantities are the frequency resolved electrical impedance as well as the spatially and frequency resolved surface displacement of the investigated transducer structures.
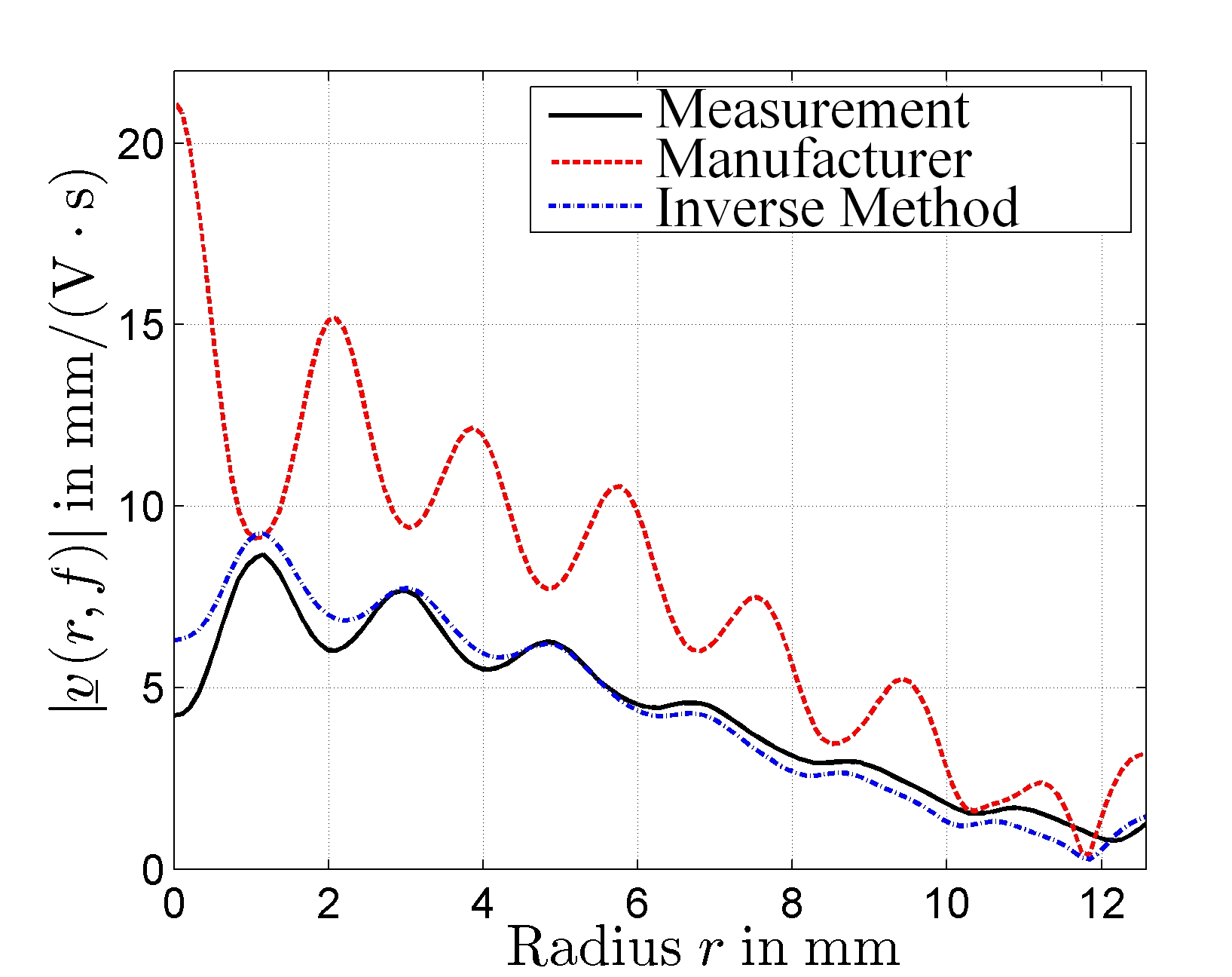 |
Figure 1:
Spatially resolved surface normal velocity for the thickness extensional mode of a piezoelectric disc made of Pz27 with 25 mm in diameter and a height of 2 mm. The numerical simulations were calculated with the material parameters provided from the manufacturer and the parameters resulting from the Inverse Method.]
|
The numerical simulation of the electrical and mechanical behavior of the composites is conducted with a problem-adapted Finite-Element-Method (FE). Thereby, the focus is on the determination of a homogenized transducer structure and modeling with higher order finite elements (isotropic and anisotropic pFEM).
The Inverse Method will be analyzed with reference to its application for different composite geometries and piezoceramics (discoidal and cuboidal shaped). Subsequently, this method will be used to determine tolerance ranges and temperature dependencies of the material parameters.
The description of the large signal behavior will be carried out with a Preisach-based hysteresis model. Thereby, nonlinear mapping functions between the corresponding mechanical and electrical quantities are determined. This is a phenomenological process. The key benefit of this method is the low computational effort compared to other hysteresis modeling methods.
|
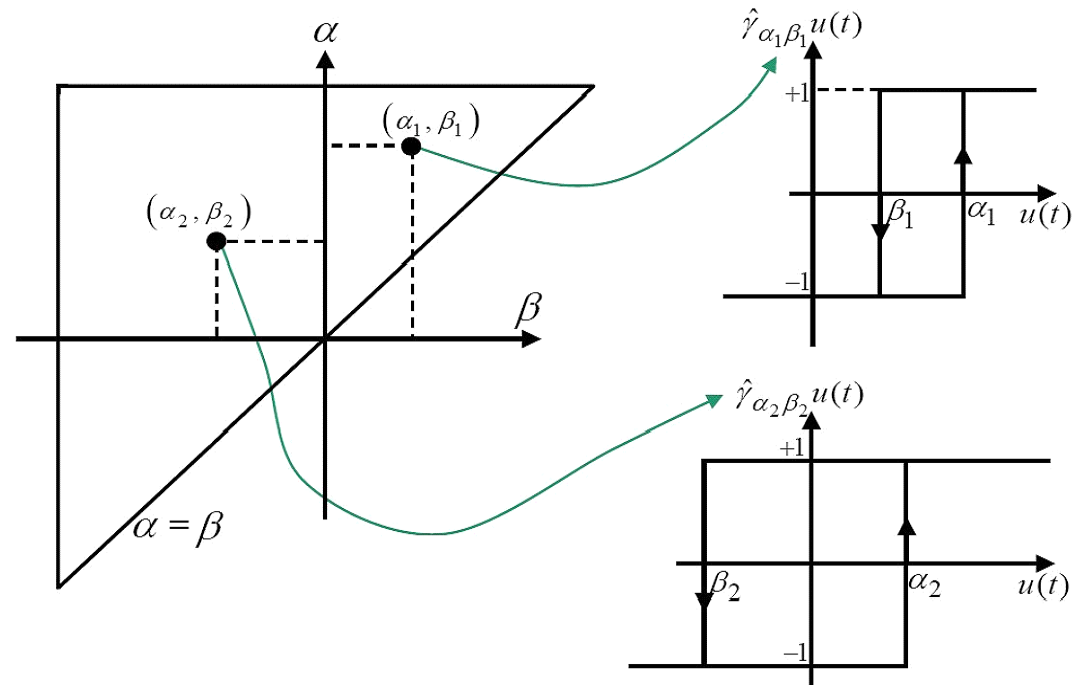 |
|
Figure 2a: Preisach plane, α and β are switching points
of the Preisach operator |
|
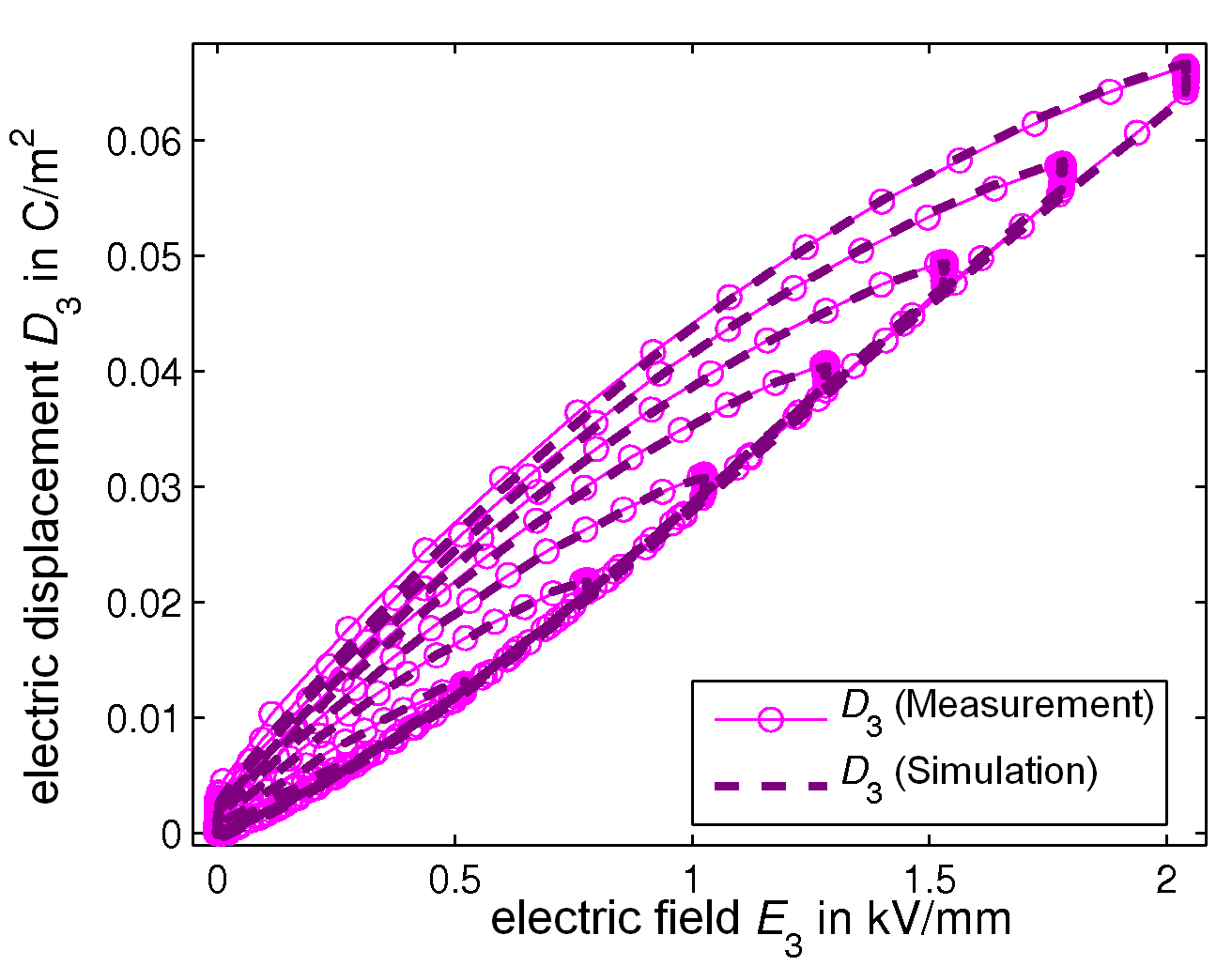 |
|
Figure 2b:
Electric displacement versus electric field |
|
|
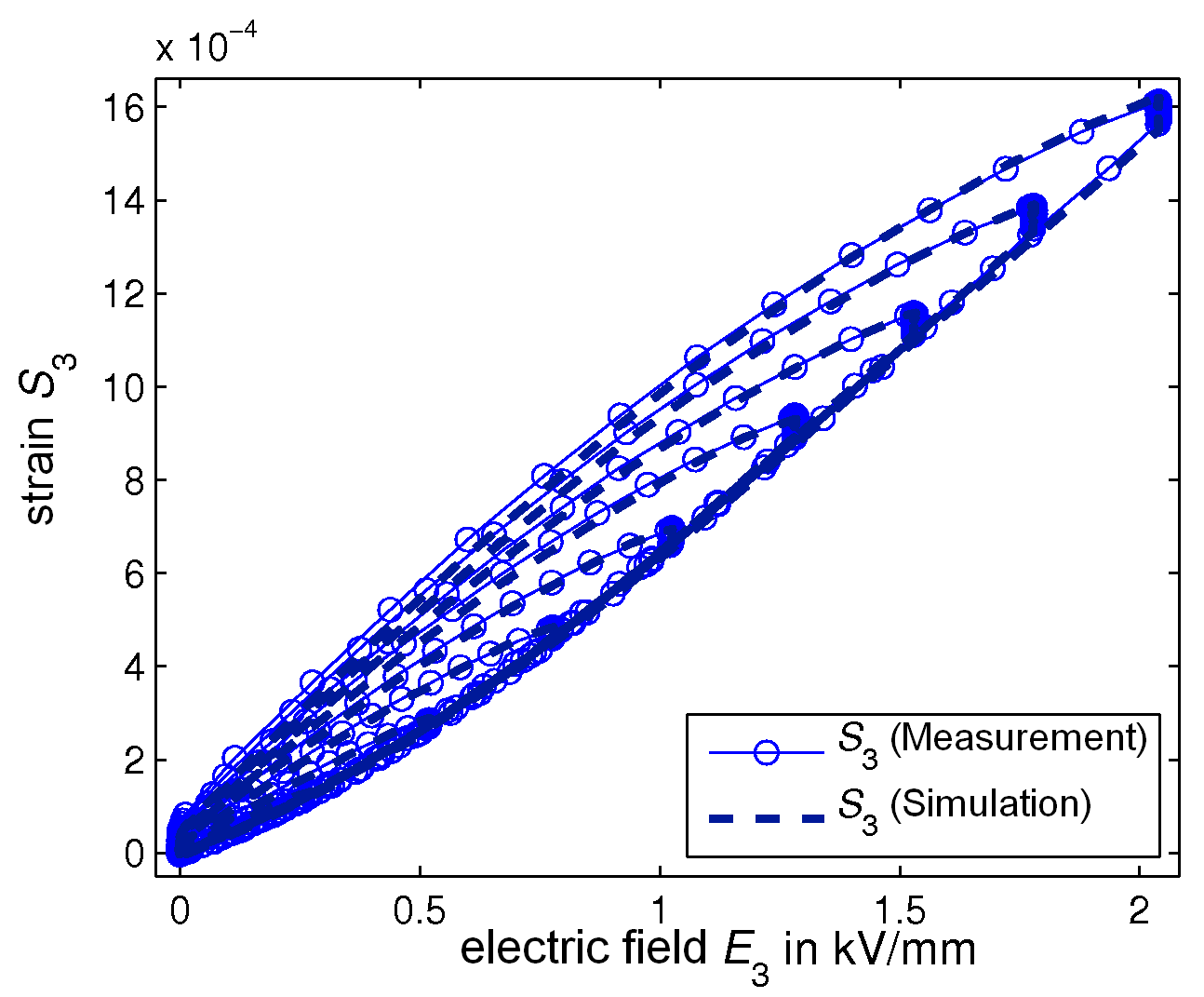 |
|
Figure 2c:
Strain versus electric field] |
|