Teilprojekt A2
Mikrostrukturierung und Integrationstechnologie für Piezofasern in metallische Trägerwerkstoffe (Blech)
Leiter:
Prof. Dr.-Ing. Andreas Schubert
Technische Universität Chemnitz
Fakultät für Maschinenbau
Institut für Werkzeugmaschinen und Produktionsprozesse
Professur Mikrofertigungstechnik
09107 Chemnitz
Telefon: 0371 / 531 34580
Telefax: 0371 / 531 23549
E-Mail: andreas.schubert@mb.tu-chemnitz.de
Prof. Dr.-Ing. habil. Prof. E. h. Dr.-Ing. E. h. Dr. h. c. Reimund Neugebauer
Technische Universität Chemnitz
Fakultät für Maschinenbau
Institut für Werkzeugmaschinen und Produktionsprozesse
Professur Werkzeugmaschinen und Umformtechnik
09107 Chemnitz
Telefon: 0371 / 531 23500
Telefax: 0371 / 531 23509
E-Mail: wzm@mb.tu-chemnitz.de
Dr.-Ing. Hans-Joachim Koriath
Technische Universität Chemnitz
Fakultät für Maschinenbau
Institut für Werkzeugmaschinen und Produktionsprozesse
Professur Werkzeugmaschinen und Umformtechnik
09107 Chemnitz
Telefon: 0371 / 531 23500
Telefax: 0371 / 531 23509
E-Mail: wzm@mb.tu-chemnitz.de
Motivation und Forschungsbedarf
Das Teilprojekt A2 verfolgt dabei den innovativen Ansatz einer Integration stabförmiger Piezoelemente in durch Umformverfahren mikrostrukturierte Aluminiumbleche. Die Besonderheit gegenüber allen bisher bekannten Technologien besteht in der direkten Anbindung der Piezoelemente in einem Blechhalbzeug durch Kraft- und Formschluss ohne elastische Zwischenschichten.
![]() |
![]() |
|
Bild 1: Explosionsgrafik eines Piezo-Metall-Moduls mit direkt integrierten Piezo-elementen in mikro-strukturiertem Aluminium-Blech |
Bild 2: Demonstrator des Piezo-Metall-Moduls mit 10 einzelnen Piezostäben in mikro-strukturiertem Aluminiumblech (Ergebnis 1. Förderzeitraum) |
Das Konzept des Piezo-Metall-Moduls ist in Bild 1 schematisch dargestellt. Dieser Piezo-Metall-Modul nutzt den piezoelektrischen Longitudinaleffekt (d33-Effekt). Die Übertragung der mechanischen Kraft erfolgt parallel zum angelegten bzw. generierten elektrischen Feld normal zu den Dünnschichtelektroden, Isolationsschichten und Kavitätswänden. Die Piezoelemente bestehen aus PZT-Keramik und besitzen eine Querschnittsfläche 0,27 x 0,27 mm² bei einer Kontaktlänge von 10 mm gegenüber den Wänden der Mikrokavitäten. Als Versuchswerkstoffe wurden für die Automobilindustrie relevante Aluminiumlegierungen (AlMg4,5Mn0,4 und AlSi1,2Mg0,4) mit Blechstärken in einem Bereich von 0,8 mm bis 1,5 mm ausgewählt. Bild 2 zeigt einen Demonstrator des Piezo-Metall-Moduls mit 10 Piezostäben, welche über flexible Leiterplatten elektrisch kontaktiert wurden.
In der ersten Förderperiode wurden grundlegende Technologien für die serienfähige Herstellung von Mikrostrukturen mittels Durchsetzen und Fließpressen, die Integration einzelner stabförmiger Piezoelemente durch eine sensorgeführte Mikromontage und das Fügen durch Umformen erforscht. Die Ergebnisse dieser Arbeiten sollen im Folgenden kurz dargestellt werden.
Schwerpunkt 1: Mikrostrukturierung
Bild 3: Umformmaschine für das Mikrofließpressen (links); schematische Darstellung des Fließpresswerkzeuges (Mitte);
Detailfoto des modularen Werkzeugstempels (rechts)
Bild 4: Beispielhafte Umformergebnisse zum Fließpressen von Mikrokavitäten in AlMg4,5Mn0,4 bei einer Maximalkraft
von 90 kN und einer Ausgangsblechdicke von 0,8 mm
Schwerpunkt 2: Integrationstechnologie
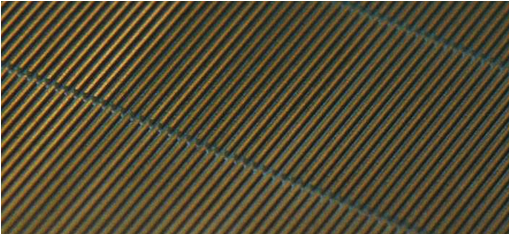
Bild 5: Piezostäbe (Abmaße ca. 0,27 mm x 0,27 mm x 15 mm) auf Klebefolie
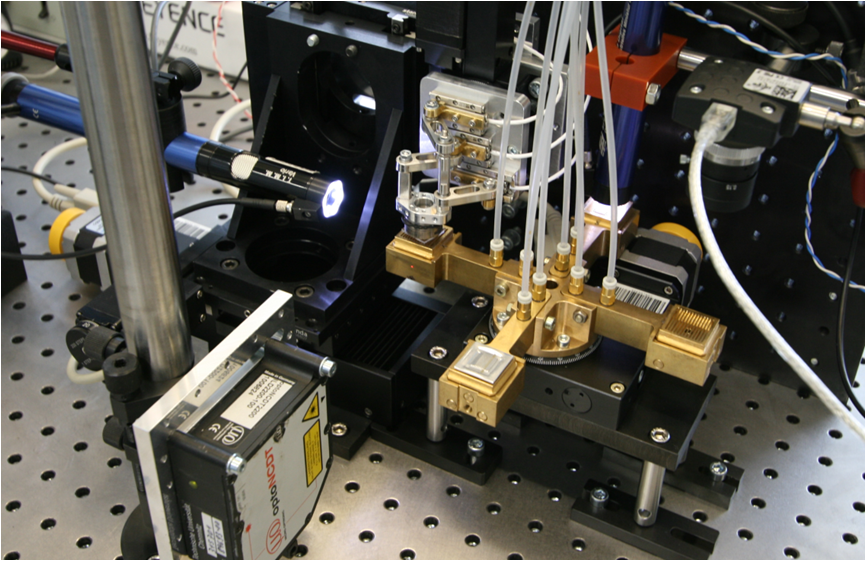
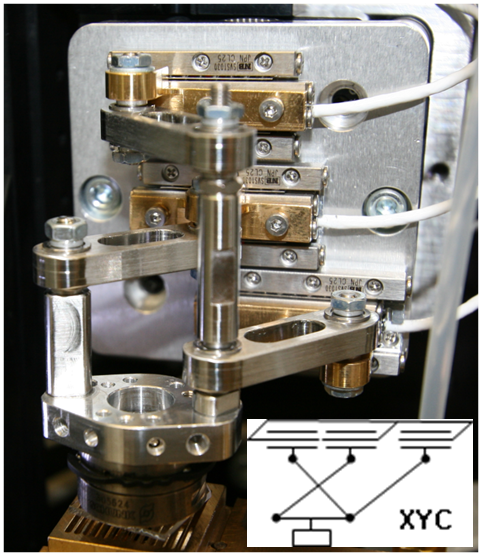
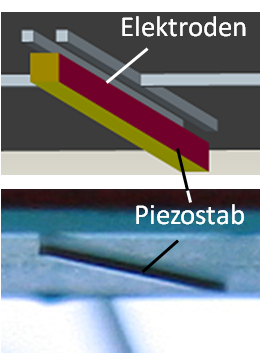
Bild 6: Modulare Versuchseinrichtung für Mikromontage mit Miniatur-Triglide-Parallelkinematik (links)
und Planarer elektrostatischer Mikrogreifer mit Piezostab
Schwerpunkt 3: Fügetechnologie
Bild 7: Beispielhafte Ergebnisse zum Fügen von Piezoelementen in metallische Trägerkavitäten (ALMg4,5Mn0,4 d = 1,5 mm)
und Simulation der mechanischen Spannungen im gefügten Piezoelement (rechts)
Innerhalb der aktuellen Förderperiode besteht der Forschungsbedarf nun vor allem in der Weiterentwicklung der Produktionstechnologien mit Blick auf die Großserienfähigkeit. Statt der Integration einzelner Piezoelemente, die im ersten Antragszeitraum für die Grundlagenuntersuchungen verfolgt wurde, sollen zukünftig vollständig kontaktierte und isolierte Verbunde aus stabförmigen Piezoelementen, „Piezo-Sprossen-Verbunde“ (PSV), gefertigt und integriert werden. Daraus ergeben sich wesentliche neue Forschungsschwerpunkte in Bezug auf die Mikrostrukturierung und Integrationstechnologie.
Zielsetzung
Das Teilprojekt gliedert sich in vier Forschungsschwerpunkte:
1. Weiterentwicklung von Technologien zur prozesssicheren umformtechnischen Mikrostrukturierung des Trägermaterials (Federführung Prof. Schubert)
2. Entwicklung von Fertigungstechnologien für Piezo-Sprossen-Verbunde (PSV) aus Piezoplatten (Federführung Prof. Neugebauer/ Dr. Koriath)
3. Entwicklung von Anlagentechnik für die Handhabung und Präzisionsmontage von Piezoplatten und PSV (Federführung Prof. Neugebauer/ Dr. Koriath)
4. Verfahrensentwicklung zum umformtechnischen Fügen von Piezoelementen in mikrostrukturierte Trägerwerkstoffe (Federführung Prof. Schubert)
Bild 8: Schematische Darstellung des Aufbaus des Piezo-Metall-Moduls aus
komplexen Mikrostrukturen in Aluminium-Blech und Piezo-Sprossen-Verbund
Methoden
Bild 9: Konzept zur Herstellung von Piezo-Metall-Modulen mit Piezo-Sprossen-Verbunden (PSV)
Ausgangsmaterial für die Fertigung von PSV sind durch das TP A1 bereitgestellte Faser-Komposit-Platten welche durch das TP A3 elektrodiert und partiell mit einer Isolationsschicht versehen werden. Die Entwicklung einer Technologie für die Fertigung von PSV aus diesen Platten ist Gegenstand der Forschungsarbeiten des TP A2. Das Aufbringen der Sammelelektrode und der vollständigen Isolation der PSV (in Bild 4 nicht dargestellt) erfolgt durch die TP A4 und A3 bzw. durch das TP A6. Die Erforschung von Technologien für die Herstellung der komplexen Mikrostrukturierung des Trägerwerkstoffes, das Einlegen der PSV und das Fügen sind wiederum Gegenstand des TP A2. Anschließend erfolgt die Kontaktierung durch das TP A4 sowie die Umformung des Moduls durch TP B1 und die Polarisation durch das TP C3.
Die Technologien zur Mikrostrukturierung werden dahingehend weiterentwickelt, dass neben den Kavitäten zusätzlich Substrukturen zur Integration der Sammelelektroden sowie Formelemente wie beispielsweise Kegelstümpfe zur definierten Lagezuordnung und Montage der PSV in den Trägerwerkstoff mittels Mikrofließpressen und/oder Mikrodurchsetzen eingebracht werden können. Dazu werden die im ersten Antragszeitraum entwickelten modularen Werkzeugsysteme zum Mikrofließpressen und Mikrodurchsetzen überarbeitet und eingesetzt. Durch systematische Untersuchungen soll der Einfluss der Prozesseingangsgrößen bezüglich der erzielbaren Abbildegenauigkeiten, Strukturgeometrien und Oberflächenqualitäten ermittelt und bewertet werden. Durch eine Kombination der Umformtechnologien Fließpressen und Durchsetzen soll die Geometrievielfalt erhöht und komplexere Mikrostrukturen hergestellt werden. Schließlich soll auch der Nachweis zur Reproduzierbarkeit der Einzelverfahren und Verfahrenskombinationen erbracht werden.
Für die Herstellung der PSV werden verschiedene Fertigungskonzepte und erarbeitet und untersucht. Schwerpunkte der Forschungsarbeiten liegen dabei in der Prozesskettenentwicklung, der Konzeption von Komponenten für die Handhabung der empfindlichen beschichteten Piezoplatten bzw. PSV und in der Erforschung von Verfahren zum präzisen Trennen von Piezokeramik und Kompositen. Die im ersten Antragszeitraum entwickelte Anlagentechnik für die Handhabung und Mikromontage mit elektrostatischen und Vakuum Mikrogreifern wird dazu weiterentwickelt. Die Handhabungstechnik wird derart rekonfigurierbar gestaltet, dass sowohl die Handhabung der Platten zur Fertigung der PSV, als auch die Handhabung der PSV und die Integration in Module oder lokal mikrostrukturierte Großbleche auf einer entsprechend angepassten Anlage durchgeführt werden können.Für das Trennen werden Trennschleifverfahren (Innen- und Außentrennschleifen) untersucht und eingesetzt. Zur Erhöhung der Ausbeute bei der Integration und nach dem Fügen sollen neben optischen Verfahren zur Erkennung fehlerhafter PSV die inhärenten Sensorfunktionen des Moduls bzw. der PSV genutzt werden.
Die geplante Anlagentechnik wird die Herstellung einer Vielzahl von Versuchsmustern der Piezo-Metall-Module ermöglichen, welche dann zunächst für weiterführende Untersuchungen im Bereich des Fügens zur Verfügung gestellt werden. Diese zielen auf die Charakterisierung der Fügeverbindung ab. Insbesondere die Ermittlung bzw. Kenntnis der auf die Piezoelemente wirkenden Druckspannungen ist für den weiteren Prozessschritt „Polarisation“ notwendig. In systematischen Untersuchungen sollen aufbauend auf den Ergebnissen der 1. Antragsphase weiterführende experimentelle Untersuchungen zur Bewertung des Einflusses strukturierter Zwischenstege an spanend und später umformtechnisch hergestellten Proben durchgeführt werden. Durch den Abgleich der Ergebnisse aus Simulation und Experiment sollen die Kontaktspannungen, d.h. die auf die Piezoelemente wirkenden mechanischen Spannungen bestimmt werden. Das Ziel ist hierbei reproduzierbare Fügeverbindung mit definierter Vorspannung zu erzeugen.