Teilprojekt B3
Gießtechnische Integration piezokeramischer Module in metallische Bauteile - Verfahrenstechnische Grundlagen und numerische Simulation
Leiter/in:
Prof. Dr.-Ing. Robert F. Singer
Friedrich-Alexander Universität Erlangen-Nürnberg
Lehrstuhl für Werkstoffkunde und Technologie der Metalle
Martensstraße 5
91058 Erlangen
Telefon: 09131 / 85 27530
Telefax: 09131 / 85 27515
E-Mail: robert.singer@ww.uni-erlangen.de
Prof. Dr.-Ing. habil. Carolin Körner
Friedrich-Alexander Universität Erlangen-Nürnberg
Lehrstuhl für Werkstoffkunde und Technologie der Metalle
Martensstraße 5
91058 Erlangen
Telefon: 09131 / 82 27528
Telefax: 09131 / 85 27515
E-Mail: carolin.koerner@ww.uni-erlangen.de
Ansprechpartner:
Dipl.-Ing. Matthias Schwankl
Universität Erlangen-Nürnberg
Lehrstuhl Werkstoffkunde und Technologie der Metalle
Martensstr. 5
91058 Erlangen
Telefon: 09131 / 85 27768
Telefax: 09131 / 85 27515
E-Mail: Matthias.Schwankl@ww.uni-erlangen.de
Dipl.-Ing. Alexander Klassen
Universität Erlangen-Nürnberg
Lehrstuhl Werkstoffkunde und Technologie der Metalle
Martensstr. 5
91058 Erlangen
Telefon: 09131 / 85 28748
Telefax: 09131 / 85 27515
E-Mail: alexander.klassen@ww.uni-erlangen.de
Ziel des Teilprojekts B3 im SFB/TR 39 ist die Integration piezokeramischer Sensor-Aktor-Module in metallische Bauteile in einem Druckgießprozess. Das Druckgießen ist für die Verarbeitung von Aluminium- und Magnesiumlegierungen zu komplexen Bauteilen in hervorragender Weise geeignet. Insbesondere zeichnet es sich aufgrund seiner kurzen Zykluszeiten durch eine hohe Wirtschaftlichkeit bei Großserienfertigung aus. Aus den Vorteilen erklärt sich die heute dominierende Stellung des Druckgusses bei der gießtechnischen Verarbeitung von Leichtmetalllegierungen.
Die wesentliche Herausforderung bei der Piezomodulintegration besteht in der Beherrschung der thermo-mechanischen Beanspruchung der Module im Zuge der Formfüllung und Abkühlung. Den Lösungsweg für die schädigungsfreie Integration stellt im vorliegenden Projekt eine Ummantelung der Module mit einer hochporösen Struktur dar. Die Struktur soll einerseits durch eine möglichst homogene Stützwirkung die auf den Modul wirkenden lokalen Kräfte minimieren und eine exakte Positionierung erlauben. Andererseits sollte keine negative Beeinflussung der Gussmatrix durch die eingebettete Stützstruktur hervorgerufen werden und die Struktur muss sehr gut mit Aluminiumschmelze penetrierbar sein.
Im bisherigen Projektverlauf wurden erfolgreich Ummantelungskonzepte erarbeitet, welche die vollständige Integration piezokeramischer Module bei erhaltener Funktionalität erlauben. Als Stützstruktur für die Module in der Form wird Streckmetall aus Al99,5 eingesetzt (Bild 1). Dieses besitzt eine hohe Steifigkeit, lässt sich hervorragend mit Metallschmelze penetrieren und erlaubt eine relativ exakte außermittige Modulpositionierung. Mit diesem Konzept bedarf es zudem keiner speziellen Anpassung der Druckgießparameter wie Druck oder Geschwindigkeit.
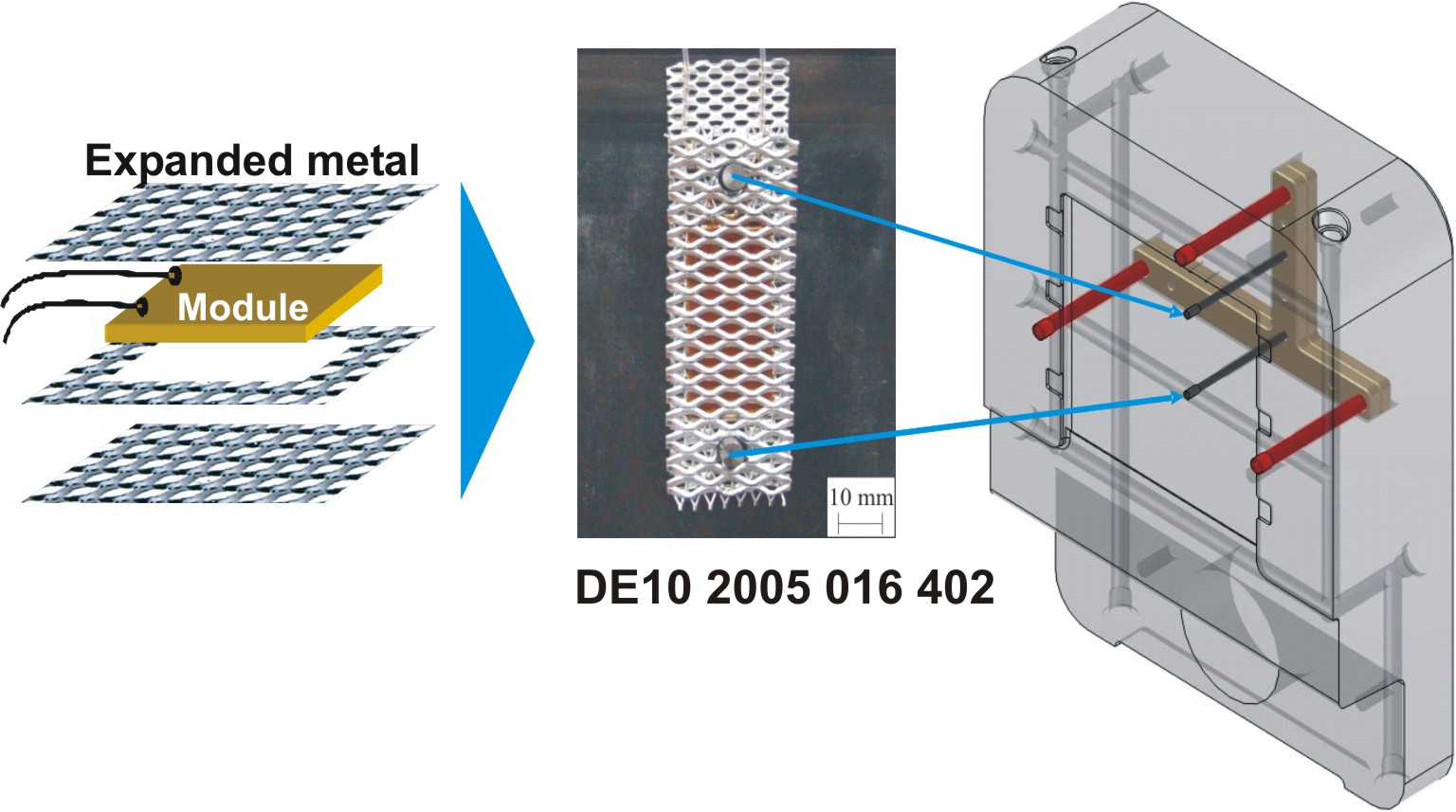
Bild 1: Der piezokeramische Modul wird zur Abstützung und zur Positionierung mit
Streckmetall ummantelt und anschließend auf Auswerferstifte in die Kavität
des Druckgusswerkzeugs appliziert.
Bild 2: Gussteil mit integriertem piezokeramischen Modul (rote Markierung).
Der Modul, der wie das Durchstrahlbild zeigt durch den Eingießprozess
nicht geschädigt wurde, kann direkt kontaktiert werden.
Auf experimenteller Seite soll die Funktionalität der aktiven Struktur durch exakte Modulpositionierung fern von der neutralen Faser weiterentwickelt werden. Gleichzeitig soll die Bauteilbeeinflussung durch Reduzierung des Stützstrukturvolumens und Verbesserung der Verbundeigenschaften von Matrix und Stützstruktur minimiert werden. Dazu werden verschiedene Ansätze verfolgt, insbesondere sollen an die jeweilige Formfüllsituation angepasste Stützstrukturen und auch geeignete Beschichtungen zur Oberflächenaktivierung entwickelt werden. Durch die Beschichtungen und die daraus resultierenden Reaktionen mit der Gussmatrix soll die Bildung einer stoffschlüssigen Verbindung zwischen Stützstruktur und Matrix realisiert werden.
Als maßgebende Größe für die schädigungsfreie Integration der Module ist die hohe Dynamik der in den Formhohlraum einströmenden Schmelze zu sehen. Das numerische Modell (Bild 3 und 4), welches aktuell mit Hilfe der kommerziellen Software Flow-3D erstellt wird, soll es zukünftig ermöglichen, die Kräfteverteilung innerhalb der Kavität auszulesen. Auf Basis der gewonnenen Erkenntnisse soll gezielt die Auslegung der Modulfixierung und der Positionierung des Modulpaketes im Werkzeug erfolgen.
![]() |
![]() |
Bild 3: Sensor-Aktor-Modul und Streckmetall zur Fixierung der Module in der Werkzeugkavität (oben). Schematische Darstellung der einzelnen Komponenten für die numerische Simulation (unten) |
Bild 4: Schema der Formfüllsimulation mit den Schwerpunkten Formfüllung und Streckgitter-Infiltration |
Bild 5: Simulation der Aufschrumpfung der Aluminiummatrix (orange) auf den Modul (blau).
Zwischen Modul und Matrix entsteht ein Spalt, der lokal zu einer messbaren Wölbung
auf den Realbauteilen führt. Die Wölbung kann über eine Auswertung der Oberflächen-
topographie nachgewiesen werden.