Arbeitsgruppen
Koordinator Arbeitsgruppenarbeit:
PD Dr.-Ing. Welf-Guntram DrosselFraunhofer-Institut für Werkzeugmaschinen und Umformtechnik (IWU)
Reichenhainer Str. 88
09126 Chemnitz
Telefon: 0371 / 5397 1304
Telefax: 0371 / 5397 1447
E-Mail: drossel@iwu.fraunhofer.de
Ziel der Arbeitsgruppe Umformen ist die Herstellung eines intelligenten Halbzeuges, d. h. eines Halbzeugs mit einer integrierten Sensor- und Aktorfunktionalität sowie dessen Umformung zu einem Strukturbauteil. Das Umformen erfolgt dabei unter Realisierung einer schwimmenden Lagerung der Piezomodule, mittels eines sich während des Umformens noch im niedrigviskosen Zustand befindlichen Klebstoffes (TP B1). Die Aushärtung des Klebstoffes erfolgt erst nach der Umformoperation.
Neben kommerziellen Piezomodulen werden zukünftig verstärkt projektinterne Piezomodule integriert. Diese Module werden durch die Teilprojekte A2, A5 und A6 bereitgestellt. Es handelt sich dabei um mikrostrukturierte Piezo-Metall-Module (TP A2), thermoplastverbundkompatible Piezokeramik-Module (TP A5) und µIM-Piezomodule (TP A6).
TP C3 entwickelt dabei die Polarisationstechnologie dieser Piezomodule. Die Kontaktierung der Module erfolgt in enger Zusammenarbeit mit TP A4. Der Umformvorgang wird in TP B2 abgebildet, wobei ein Schwerpunkt der Simulation auf die Ermittlung der Belastung des Piezomoduls gerichtet ist.
Der Aushärtevorgang des Klebstoffes wird in TP C7 durch ein eigens entwickeltes Materialmodell beschrieben, welches zukünftig in das globale Simulationsmodell aus TP B2 integriert werden soll. Eine anschließende Funktionsprüfung umgeformter Piezo-Metall-Verbunde bzw. die Bestimmung der Degradation erfolgt in den Teilprojekten B1, B2 und C8.
Welche Auswirkungen der Umformvorgang auf die Polarisation der integrierten Piezomodule hat, wird in den Teilprojekten C3 und C8 untersucht. Die Ergebnisse aus Experiment und Simulation fließen in die Weiterentwicklung der projektinternen Module ein. Die Grenzen der Umformbarkeit werden für verschiedene Piezomodule und Prozessparameter ermittelt.
![]() Bild 1: Prozesskette Umformen |
||
TP A5 |
TP B1 | |
![]() |
![]() |
|
Bild 2: Prototypisches thermoplastverbundkompatibles Piezokeramik-Modul (TPM) auf Polyamid-Basis |
Bild 3: Herstellung Rechtecknapf durch Tiefziehen, Umformung im viskosen Klebstoffzustand ermöglicht doppelte Krümmung des Piezomoduls |
|
TP C7 | TP B2 | |
![]() |
![]() |
|
Bild 4: Simulation des Aushärtevorgangs von Klebstoffen, Viskoelastische Materialmodellierung in Abhängigkeit von Aushärtegrad q und Temperatur |
Bild 5: Numerische Untersuchung: Tiefziehbauteil mit integriertem Piezo-Aktor - gefertigt aus intelligentem Blechhalbzeug; links: Experiment, rechts: numerische Simulation | |
Die Arbeitsgruppe Guss beschäftigt sich mit der gießtechnischen Integration von piezokeramischen Modulen in Aluminiumdruckgussbauteile. Aufgrund der hohen thermischen und mechanischen Belastungen beim Druckgießen ergibt sich eine Vielzahl von wissenschaftlichen Fragestellungen.
Bild 1: Prozesskette Guss
Um den thermischen Belastungen beim Gießen Rechnung zu tragen, werden in Teilprojekt A1 piezokeramische Laminate auf Basis von PZT-Platten in LTCC-Multilayern entwickelt, siehe Bild 2. Hier ersetzt die LTCC-Schicht die normale Polymerummantelung, welche bei zu hoher thermischer Belastung geschädigt bzw. zerstört wird. Auch die elektrische Kontaktierung der Module stellt eine Herausforderung dar, da Weichlote beim Gießen aufgeschmolzen werden und aufgrund der herrschenden Drücke verspritzen. Um auch hier eine robuste und prozesssichere Kontaktierung zu erreichen, werden in Teilprojekt A4 unterschiedliche Lasertechniken zur Erzeugung von schädigungsfreien Kontakten basierend auf Hartloten entwickelt.
Die mechanischen Belastungen beim Druckgießen können zu einer Schädigung der Module führen. Zudem besteht die Gefahr, dass die Module nicht in der angestrebten Position bleiben. In Teilprojekt B3 werden daher Methoden zur prozesssicheren Integration und Positionierung in Aluminiumdruckgussbauteile entwickelt, siehe Bild 3. Dabei wird das experimentelle Vorgehen durch numerische Simulation des Integrationsprozesses und der dabei entstehenden Temperatur- und Spannungsfelder unterstützt.
Mit Hilfe der Teilprojekte in Bereich C wird die Funktionalität der Module nach erfolgter Integration ins Bauteil zerstörungsfrei bewertet. Insbesondere die Messung und numerische Simulation der Impedanz (C6) geben hier Information über eine eventuelle prozessbedingt Schädigung der Module, siehe Bild 4.
![]() |
Bild 2: Vollkeramischer Modul | |
![]() |
Bild 3: Links: Numerische Simulation der gießtechnischen Integration eines Moduls, der durch ein Al-Streckgitter positioniert und gestützt wird. Rechts: Röntgendurchstrahlbild eines LTCC-PZT Moduls in einem Aluminiumdruckgussteil. Sichtbar ist die PTZ-Keramik (schwarz), die zwei Lotstellen, die Anschlusskabel und das Aluminiumstreckgitter (hellgrau) |
|
![]() |
Bild 4: Impedanzmessung an Modulen vor und nach der Integration ins Bauteil. Durch Entfernung der Gussmatrix können eventuelle Schädigungen der Module erkannt werden | |
Forschungsschwerpunkt der Prozesskette Faserkunststoffverbunde ist die seriengerechte Herstellung aktiver Strukturbauteile in Faserverbundbauweise durch den Einsatz thermoplastverbundkompatibler Piezokeramik-Module (A5, B4) sowie durch die direkte stoffliche Integration piezokeramischer Komponenten in Polyurethanverbunde mittels neuartiger Multi-Faser-Sprühtechnologie (B6). Hierfür werden sowohl bisherige kommerziell verfügbare Moduldesigns stofflich auf ein thermoplastisches Materialsystem umgestellt als auch neuartige piezokeramikfaserbasierte Module entwickelt (A5, A1). Neben der Frage der stofflichen Kompatibilität werden vor allem Fragen einer ganzheitlichen Gestaltung der Prozesskette untersucht. Dies schließt z.B. auch Fragen einer bauteilinhärenten Gestaltung von Leiterbahnen und Kontakten zur Energie- und Informationsübertragung mit ein (A4, A5, B4).
Der Nachweis der Bauteilfunktion und der durchgängigen werkstofflich homogenen Anbindung vom Modulhalbzeug an die Verbundstruktur erfolgt am Beispiel einer PT-PIESA-Einheitsplatte (C6). Anhand der erarbeiteten Modelle zum Polarisationsverhalten piezokeramischer Werkstoffe unter Temperatur- und Druck-einfluss kann die Rückwirkung einer thermo-mechanischen Belastung auf den Polungsprozess beschrieben und eine effiziente Verlagerung des Polungsprozesses in die Bauteilfertigung (Formgebung und Konsolidierung) vorgenommen werden (C3, B4). Zum Nachweis der Schädigungsfreiheit bzw. zur Analyse des Schädigungszustandes aktiver Faserverbundstrukturen wird ein zerstörungsfreies Prüfverfahrens auf Basis des pyroelektrischen Effektes entwickelt (C8).
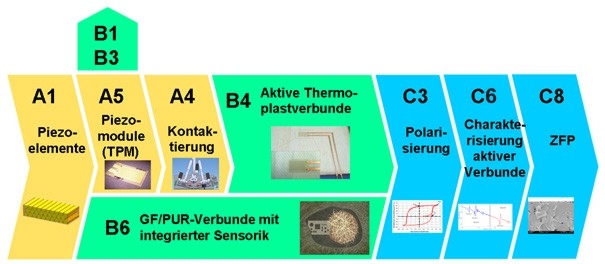
Bild 1: Prozesskette Faserverbundtechnologien
Die Arbeitsgruppe Piezokeramik und Charakterisierung beschäftigt sich mit der Auslegung, Fertigung und Charakterisierung von piezokeramischen Komponenten für die Integration in Leichtbaustrukturen. Ausgehend von den Anforderungen der Prozessketten, werden insbesondere Themen zur Materialauswahl, zu Design-Richtlinien und zur Charakterisierung effektiver Materialkenndaten diskutiert. Dabei stehen Piezomodule auf Basis piezokeramischer Fasern und Platten im Vordergrund.
Piezofaser-Komposite bestehend aus piezokeramischen Fasern in einer Polymermatrix werden vor allem in den Prozessketten Blechumformung und Faserverbund eingesetzt. Hier spielen Fragen zur Geometrie und Anordnung der Fasern im Polymer, zur Faser-Matrix-Haftung sowie zur Ansteuerung der Komposite eine entscheidende Rolle.
Piezokeramische Laminate auf Basis von PZT-Platten in LTCC-Multilayern finden vor allem in der Prozesskette Gießen im Aluminiumdruckguss Anwendung. Der Fokus liegt hier in der stoff- und formschlüssigen Integration, der mechanischen Klemmung der Module durch das umgebende Metall und der Weiterkontaktierung der Module.
Ein besonderer Schwerpunkt der Arbeitsgruppe liegt in der Ermittlung und Auswertung effektiver Materialkenndaten. Messungen des Polarisationszustandes, der Auslenkung, der elektrischen Impedanz und des Pyrostromes an Modellstrukturen unter Mehrfeldbelastungen werden mit effektiven Materialdaten integrierter Piezomodule aus den Prozessketten verglichen und bewertet.
Die Arbeitsgruppe setzt sich aus Mitgliedern aller Prozessketten zusammen und trifft sich je nach Schwerpunktthema ein- bis zweimal jährlich.
![]() |
![]() |
|
Bild 1::REM-Aufnahme eines Querschliffs von PZT-Fasern in Polymermatrix |
Bild 2: Röntgenstrukturaufnahme eines LTCC/PZT-Moduls |
|
![]() |
![]() |
|
Bild 3: Messaufbau zur Charakterisierung von piezokeramischen Materialien |
Bild 4: Messaufbau zur Charakterisierung der pyroelektrischen Antwort mittels thermischer Wellen |