Teilprojekt A6
Fertigungstechnologien für Piezomodule mit integrierten Keramikfaser-Kompositen und Funktionspolymeren zum Einsatz in aktiven metallischen Bauteilen
Leiter:
Prof. Dr.-Ing. habil. Lothar Kroll
Technische Universität Chemnitz
Institut für Allgemeinen Maschinenbau und Kunststofftechnik
Professur Strukturleichtbau und Kunststoffverarbeitung
Reichenhainer Str. 70
D-09126 Chemnitz
Telefon: 0371 / 531 - 38081
Telefax: 0371 / 531 - 23129
E-Mail: lothar.kroll@mb.tu-chemnitz.de
Darstellung des Forschungsprogramms
Motivation
Die zunehmende Miniaturisierung von Produkten mit elektronischen und mechatronischen Baugruppen zwingt zur größtmöglichen Funktionsintegration und Entwicklung von Fertigungstechnologien für sehr kleine Mehrkomponenten-Bauteile. Hierzu ist die Mikrospritzgießtechnologie für kunststoffbasierte Kleinstteile hervorragend geeignet. Durch die Mikrospritzgießtechnik können Kunststoffteile mit hoher Formenfreiheit nachbearbeitungsfrei in hohen Stückzahlen gefertigt werden. Dabei erlaubt die Flexibilität des Verfahrens die Kombination verschiedener elektrisch leitender und isolierender Materialien sowie die Integration von piezokeramischen Einlegern zur Ausbildung von elektromechanischen Wandlermodulen.
Die Untersuchungen aus dem ersten Antragszeitraum des TP A6 zeigen dabei die prinzipielle Funktionstauglichkeit eines piezokeramischen Generators, der eingebettet in einer Kunststoffmatrix das elektromechanische Verhalten am Beispiel einer aktiven Biegestruktur zeigt. Darüber hinaus konnte nachgewiesen werden, dass die Kontaktierung der piezokeramischen Faserkomposite (PFK) und die Weiterleitung der erzeugten Ladungen durch elektrisch leitfähige kohlenstofffaserverstärkte Kunststoffe (CFK) mit Duroplastmatrix grundsätzlich möglich sind.
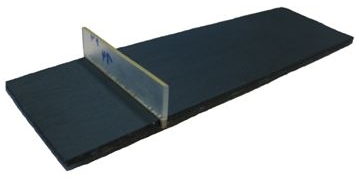
a) |
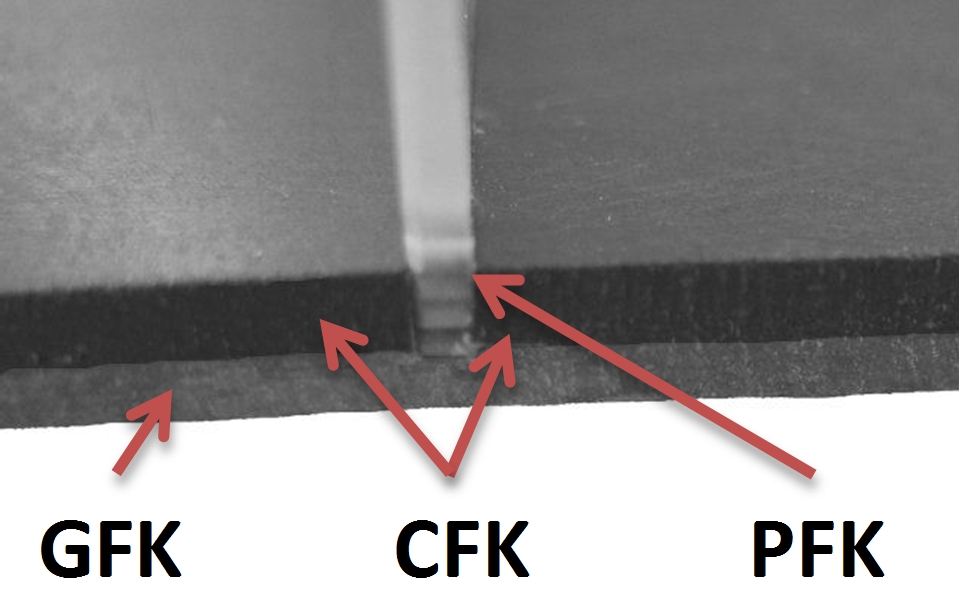
b) |
Bild 1: a) aktive Biegestruktur mit integrierten piezokeramischen Faserkompositen (PFK)
b) Aufbau der aktiven Biegestruktur; GFK – glasfaserverstärkter Kunststoff,
CFK – kohlenstofffaserverstärkter Kunststoff, PFK – piezokeramische Faserkomposite
Zielsetzung
Aufbauend auf den Ergebnissen aus der 1. Projektphase ergibt sich im Teilprojekt A6 das wesentliche Ziel zur Erforschung einer neuen großserienfähigen Kunststofftechnologie für die Herstellung komplexer Piezomodule unter Verwendung einer 2K-Mikrospritzgießanlage (vgl. Bild 2). Dabei sollen Piezoelemente über geeignete Bestückungssysteme der Spritzgießkavität zugeführt und fixiert werden. In dem sich anschließenden Injektionsprozess wird das modulare Werkzeug mit einem elektrisch leitfähigen thermoplastischen Kunststoff gefüllt. Die so elektrisch und mechanisch verbundenen Piezokeramiken werden durch Freigabe definierter Kavitätsräume in einem nachfolgenden Einspritzprozess mit elektrisch isolierendem Kunststoff umgeben und gleichzeitig das Packaging vorgenommen. Hieraus resultieren besondere Herausforderungen an die technologische Umsetzung, wie die Auswahl elektrisch leitfähiger thermoplastischer Kunststoffe und Additive, die Positionierung und die Fixierung der Piezoelemente und die Werkzeugkonstruktion. Die so hergestellten µIM-Piezomodule sollen in einer weiteren Spritzgießstufe in eine thermoplastische Umhüllung eingebettet werden, um sie zwischen Metallschichten für die Weiterverarbeitung in der Prozesskette „Umformen“ vorzubereiten. Einen wesentlichen Forschungsschwerpunkt bildet die Simulation des Spritzgießprozesses sowie der hybriden Modulstruktur infolge herstellungsbedingter thermischer Belastung. Auf Basis der Simulationsergebnisse erfolgt eine Sensitivitätsanalyse zur Einstellung optimaler Prozessfenster für den 2K-Mikrospritzguss.
Bild 2: Funktionsprinzip der 2K-Mikrospritzgießanlage "Microsystem 50" (Wittmann/Battenfeld)
Methoden
Die geplante Entwicklung von Fertigungstechnologien für Piezomodule mit integrierten Piezofaserkompositen (PFK) und Funktionspolymeren für die Weiterkontaktierung und Verbindung von Piezo-Komponenten erfordert die Klärung werkstofftechnischer, strukturmechanischer und prozessrelevanter Fragestellungen und die Bereitstellung geeigneter Handhabe- und Werkzeugtechnik. Zu den besonderen wissenschaftlich-technischen Herausforderungen bei der technologischen Umsetzung der neuen µIM-Piezomodule zählen insbesondere: die Auswahl bestmöglicher thermoplastischer Werkstoffsysteme und elektronischer additiver Füllstoffe, die Positionierung von Piezoelementen in der Werkzeugkavität sowie die Konstruktion und Fertigung geeigneter modularer Werkzeugsysteme. Die Festlegung angepasster elektrisch leitfähiger Kunststoffe setzt grundlegende werkstofftechnische Untersuchungen zu den Füllstoffen und deren Einfluss hinsichtlich des Füllstoffgehaltes, Partikelgröße und -form auf die Leitfähigkeit voraus. Für die Modifizierung des Spritzgießverfahrens sind die Prozessfolgen: Werkzeugpositionierung und -fixierung der Piezokeramiken, Hinter- und Umspritzung der thermoplastischen Kontaktierung und Verbindung sowie spritzgießtechnische Isolierung unter Berücksichtigung der Wärmeführung aufeinander abzustimmen. Die favorisierten Bauvarianten (siehe etwa Ausführungsbeispiel in Bild 3) sind konstruktiv umzusetzen und an das µIMP-Werkzeug anzupassen.
Bild 3: Biegewandlermodul als Ausführungsbeispiel eines µIM-Piezomoduls
Die spritzgießtechnische 2K-Herstellung der ersten Piezomodule dient hier der Ermittlung optimaler Prozessparameter und der Abstimmung aller In-situ-Prozessschritte aufeinander. In Bezug auf theoretisch basierte Lösungsansätze zur Entwicklung der neuen µIM-Piezomodule kommt der Simulation des Spritzgießprozesses zur Formfüllung und zum Temperaturverlauf sowie der Auslegung der hybriden Modulstruktur besonderer Bedeutung zu. Für den strukturmechanischen und prozessgerechten Entwurf der µIM-Piezomodule sollen auf Grundlage von Simulationsergebnissen eingehende Fertigungsstudien und darauf aufbauenden Sensitivitätsanalysen durchgeführt und die optimalen Prozessfenster sowie die zugehörigen prozessbedingten Eigenschaften ermittelt werden. Des Weiteren sind die mechanischen Kenndaten der Einzelkomponenten des Biegewandlermoduls in Abhängigkeit von dessen konstruktiven Aufbau zu bestimmen und das Piezomodul sowie deren Funktion optimal an die metallische Struktur anzupassen. Zur Vermeidung einer großen Verzugsdeformation infolge Abkühlung sollen vor allem symmetrisch aufgebaute Piezomodule betrachtet werden, bei denen die Eigenspannungen keine versagenskritische Plattenbiegung induzieren (vgl. Bild 4).
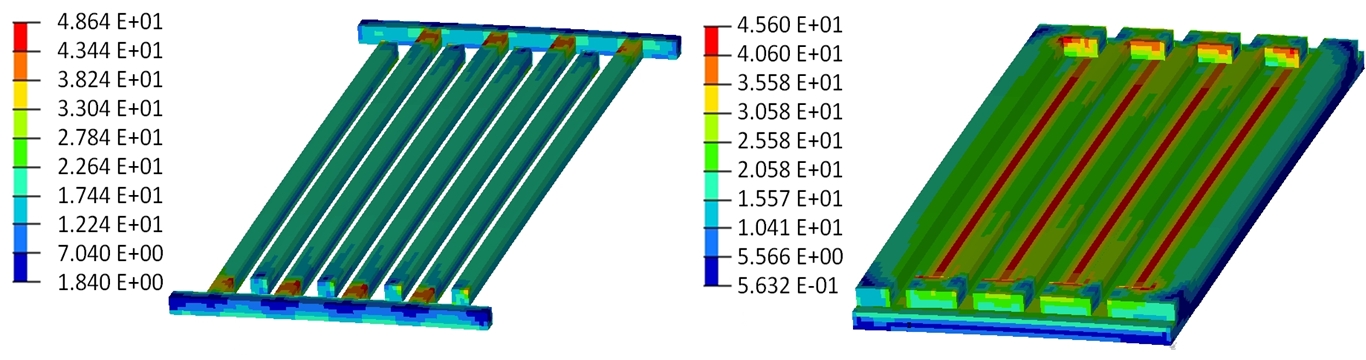
a) |
|
|
|
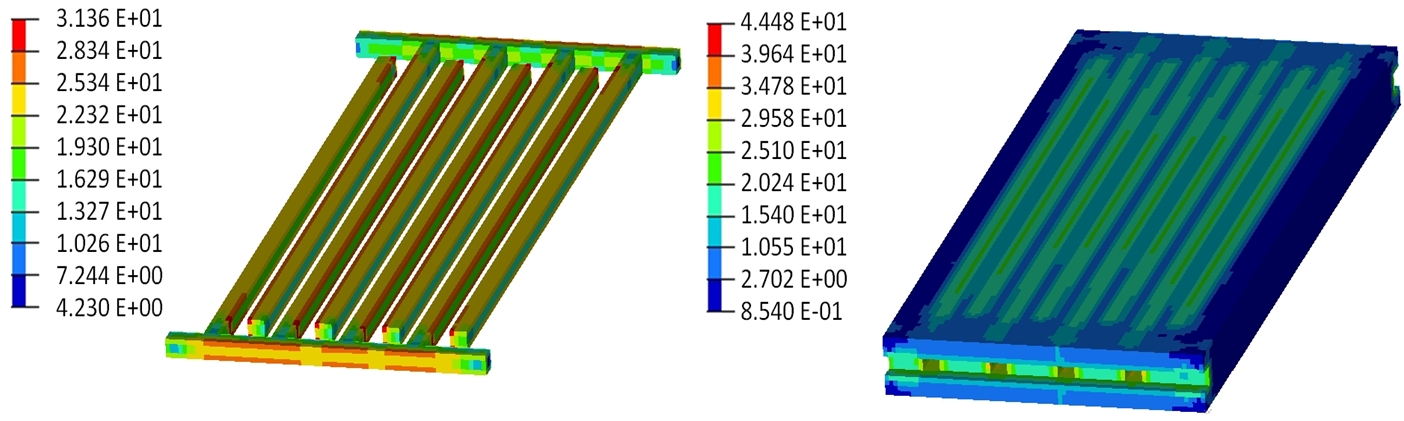
b) |
|
Bild 4: Von-Mises-Vergleichsspannungen in MPa der elektrisch leitfähigen Kunststoffkomponente und der elektrisch isolierenden Kunststoffkomponenten
für den Aufbau mit a) einer Deckschicht (asymmetrisch) sowie b) zwei Deckschichten (symmetrisch)
Um die piezoelektrischen Funktionen und die Tragfähigkeit der µIMP-Module zu gewährleisten, sind ferner numerische Berechnungen für die herrschenden spritzgießbedingten Beanspruchungsregime durchzuführen. Die hierfür notwendigen elektrischen, mechanischen und rheologischen Kennwerte sollen in werkstoffgerechten Belastungsversuchen ermittelt werden. Von besonderem Interesse sind dabei die mechanischen Eigenschaften der unterschiedlichen thermoplastischen Komponenten sowie die interlaminaren Festigkeiten der Kunststoffkombinationen und der Piezokeramik/Thermoplast-Verbindung in Bezug auf die versagensrelevante Zug- und Scherbeanspruchung infolge Schwindung.